the Creative Commons Attribution 4.0 License.
the Creative Commons Attribution 4.0 License.
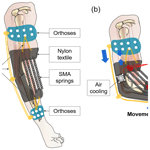
Design of a soft bionic elbow exoskeleton based on shape memory alloy spring actuators
Qiaolian Xie
Qiaoling Meng
Wenwei Yu
Rongna Xu
Zhiyu Wu
Xiaoming Wang
Hongliu Yu
Shape memory alloy (SMA) is a kind of active deformation material with a self-sensing and driving ability. It is very similar to the performance of human muscles, and through temperature changes to produce phase changes to output force and displacement, it has the ability to restore the initial shape and size. The combination of SMA and wearable robotic technology has the advantages of being light weight, energy-saving, and having great human–exoskeleton interaction. However, the existing flexible exoskeletons driven by SMA are only designed with bionic primary muscles, ignoring the role of antagonistic muscles. This study presents a novel soft bionic elbow exoskeleton based on SMA spring actuators (Sobee-SMA). The exoskeleton adopts a bionic design, combining active deformation material SMA and a high-elastic-material rubber band to simulate the contraction and relaxation of elbow skeletal muscles. Through a pulse width modulation (PWM) experiment, the driving voltage is selected as 12 V, the PWM duty cycle is 90 % during heating, and the PWM duty cycle is 18 % during heat preservation. In a relaxed state of healthy subjects, the range of motion of the elbow is about 0–80∘, and the maximum temperature is about 60–70 ∘C. During the circular movement of the elbow, the maximum temperature can be maintained within the SMA operating temperature without a high temperature. In conclusion, the exoskeleton provides elbow-assisted motion and ensures the safety of the heating process.
- Article
(3065 KB) - Full-text XML
- BibTeX
- EndNote
Strokes are one of the most common causes of disability, and stroke survivors commonly suffer impaired mobility. It has been clinically verified that long-term, repetitive, and effective rehabilitation training can help patients with upper limb dysfunction promote the recovery of motor function (Xu et al., 2020; Kwakkel et al., 1999). The existing upper limb exoskeleton rehabilitation robots (ULERRs) mostly use rigid links with external power sources, making them bulky and heavy. Although they have good robustness and movement accuracy, they cannot adapt to different sizes and physiological states of upper limbs due to their rigid structure characteristics. And the complicated mechanical structures and rigidity characteristics also weaken the bionics, wearing comfort, and portability of ULERRs. With the advancement of flexible robotics technology, flexible ULERRs have been favored by researchers due to their simple structure, flexibility, lightness, simple assembly, and low cost, and have become the current research direction of ULERRs (Xiloyannis et al., 2019a, 2021; Ang and Yeow, 2020).
As one of the most important joints in the body, the elbow is of great importance for daily activities. Existing flexible elbow exoskeleton robots are mainly divided into four driving modes: cable (Bowden cable, tendon), pneumatic, hydraulic, and smart material drives. In a cable-driven exoskeleton, cables are routed along a targeted joint and attached to anchor points on both of its sides (Xiloyannis et al., 2019b), and the motor directly transmits force and motion through the cable transmission mechanism, which has the advantages of being light weight, portable, and having good wearing flexibility. In addition, most of these mechanisms place the motor and controller on the back, so that the driving structure is far away from the joints of the human body, which can reduce the motion inertia of the extremities (Lotti et al., 2020; Xiloyannis et al., 2019b; Dinh et al., 2017). However, when force is exerted on the terminal anchor point of the human body, the muscles absorb part of the kinetic energy due to their own elasticity and then transfer it to the skeleton with larger stiffness to generate motion and force, which not only causes the problem of poor human–exoskeleton compatibility when wearing but also reduces transmission efficiency. The pneumatic and hydraulically-driven flexible elbow exoskeleton robot uses a fluid medium (gas, liquid) through the air or hydraulic pump to transfer force to the cavity of the soft composite structure, forming force and motion output (Ang and Yeow, 2020; Koh et al., 2017). Although the design of this soft composite structure solves the problems of the traditional rigid ULERRs being complex, bulky, and unable to conform to human motion, the additional driving force source and the mechanical properties of the soft composite structure also bring poor portability and control. New smart material drive methods, such as shape memory alloy (SMA) (Copaci et al., 2020; Park et al., 2020; Jeong et al., 2022), and this method are described in some detail below.
Skeletal muscles are power components of human limb movement, which has the advantages of quick response, high force-to-weight ratio, flexibility, and coordination, etc. These muscles combine the contraction and relaxation of the primary muscles and antagonistic muscles to complete the coupling driving function of biological joints. SMA is a kind of active deformation material with a self-sensing and driving ability. It is very similar to the performance of muscles, producing force and deformation through a phase transformation from martensite to austenite induced by temperature, and it has the ability to restore initial shape and size, called the shape memory effect (Villoslada et al., 2015; Jeong et al., 2022). SMA actuators use the shape memory effect to convert thermal energy into displacement or force output. This type of actuator has attracted the interest of many researchers because of its good force-to-weight ratio, simple structure, light weight, and small size, making it an ideal alternative to pneumatic, hydraulic, or motor drives. There are currently few studies on the application of SMA actuators in flexible ULERRs. The main reasons are that the directional mechanical properties of SMA actuators should conform to the motion of human arm joints (bionics) and the safety, driving efficiency, and control of ULERRs. Park et al. (2020) and Park and Park (2019) developed a flexible upper limb exosuit based on smart materials. The actuator of the exosuit is a novel fabric muscle composed of SMA springs and flexible fabric. This fabric muscle has the advantages of simple driving, softness, large force–weight ratio, flexibility, lightness, and flexibility. The fabric muscle is composed of 20 SMA springs connected in series and parallel, and it weighs only 24 g. When heated to 70 ∘C, it can generate a force exceeding 100 N, and the minimum shrinkage strain is 50 %. However, the flexible exosuit requires a high voltage with multiple SMA springs, and the cooling and control method is not mentioned. Copaci et al. (2020, 2019) developed a flexible elbow exoskeleton based on an SMA actuator. The SMA actuator is made of SMA wire, Bowden cable, and polytetrachloroethylene pipe. Among them, the SMA wire is the power element, the Bowden cable can guide the movement and transfer force, and the polytetrapairethylene is the insulator. When the SMA actuator uses a 0.02 in. diameter SMA wire, it can pull an object weighing about 3.56 kg at a high temperature (90 ∘C). The exoskeleton has no rigid component at the joint, which can better fit the changes of the axis during elbow movement, and the SMA actuator acts like a cable drive. Jeong et al. (2021, 2019) proposed a soft wearable exoskeleton to support wrist movement, with a stretchable coolant vessel-integrated SMA muscle with an active cooling system using coolant circulation. The exoskeleton can achieve wrist flexion, extension, radial deviation, and ulnar deviation with a range of motion of 38, 50, 34, and 35∘, respectively. The motion frequency of flexion and extension is 0.1 Hz, and the motion frequency of radial deviation and ulnar deviation is 0.13 Hz. Instead of a natural air cooling, the circulation of coolant can greatly improve the driving efficiency of SMA actuators and solve the slow cooling of SMA actuators. However, the weight of coolant can also increase the weight of the exoskeleton system, reducing the portability of the flexible exoskeleton, and it also necessitates consideration of the problem of coolant leakage.
Skeletal muscles combine the contraction and relaxation of the primary muscles and antagonistic muscles to complete the coupling driving function of biological joints. The primary muscle provides the driving force, and the antagonistic muscle acts as a damping to make joint motion more accurate and compliant. Therefore, both muscles are necessary for joint movement. However, the existing flexible elbow exoskeletons driven by SMA are only designed with bionic primary muscles, ignoring the role of antagonistic muscles. This paper proposes a soft bionic elbow exoskeleton based on SMA spring actuators (which can be practical at home with one power unit), which can be used for assisting elbow movement. The elbow exoskeleton combines an active deformation material (SMA) with a highly elastic material (rubber band) to simulate the contraction and relaxation of the skeletal muscles of the elbow joint. The SMA spring is a potential material for bionic muscles, and the actuators formed by SMA springs can generate a pulling force of over 48 N. When the SMA actuator contracts and actuates the elbow joint to flex, the rubber band stretches to cooperate with it, which can provide a certain damping and achieve a compliant movement. And the rubber band also provides resilience to restore the SMA actuator to its original state, enabling elbow flexion and extension.
The design of a soft bionic elbow exoskeleton based on SMA spring actuators (Sobee-SMA) is presented in Sect. 2. In Sect. 3, the control strategy and preliminary results are detailed. Sections 4 and 5 show the discussion and the conclusions of this paper, respectively.
Important factors to be considered in flexible exoskeleton design include (Pérez Vidal et al., 2021) the following:
-
Force-to-weight ratio. An actuator with a high force-to-weight ratio can meet the energy requirements of human movement and ensure the light weight of the flexible exoskeleton.
-
Portability. Portability can effectively improve the utilization rate of flexible exoskeletons, and the light-weight structure can reduce the wearer's energy consumption and improve the comfort of wearing.
-
Flexibility. Flexibility improves the comfort and adaptability of the exoskeleton. The new flexible exosuits embed actuators in soft materials, similar to normal clothes.
-
Bionics. The exoskeleton needs to simulate the characteristics of human joint movement, comply with human movement, and decrease human–exoskeleton interference movement.
-
Safety. Of all these factors, the safety of the flexible exoskeleton is of the most important, especially for patients with motor dysfunction or muscle weakness.
-
Comfort. The comfort of the exoskeleton can be considered in terms of air permeability, adaptability, flexibility, portability, and ease of loading and unloading. Comfort can also considerably enhance the utilization rate of the exoskeleton.
-
Modular. The modular exoskeleton can be adjusted according to the patient's movement ability, and the exoskeleton is simple to maintain.
-
Fixation. The design of the exoskeleton generally includes a fixation device that can fix the position of the exoskeleton and human arm. And the fixation should resist the thrust of the actuator and transfer the driving force of the exoskeleton to the body.
-
Low cost. Low-cost exoskeletons make them affordable for patients or medical institutions, and the low cost makes them family-friendly and accessible. Accordingly, exoskeletons should be designed with materials and components that are readily accessible and easily machined.
2.1 Elbow exoskeleton design based on SMA spring actuators
Skeletal muscles are the power element of human body movement. The biceps and brachialis are the major flexors of elbow, and the tricep is the major extensor of the elbow. During elbow flexion, the elbow flexor is the primary muscle. And when the opposite elbow extensor is relaxed and extended, it is the antagonist muscle during elbow flexion. Therefore, the elbow flexor and extensor muscles are a pair of primary and antagonistic muscles, which are formally opposite but are unified and coordinated for elbow motor function. When the elbow is flexed, the elbow flexor muscle contracts, and the elbow extensor muscle relaxes and stretches appropriately. When the elbow is in rapid motion, the antagonist usually contracts immediately at the end of the motion. It can prevent excessive primary movement, equivalent to the role of damping, and it can make elbow movement more accurate and compliant. In summary, the coordination of antagonistic muscles is essential for the primary muscle to complete elbow flexion, and the timely contraction of antagonistic muscles is also an important guarantee for accurate and compliant movement.
In this paper, a flexible elbow exoskeleton (Sobee-SMA) is designed to simulate the primary and antagonist muscles of elbow flexion by using SMA springs and elastic bands. The exoskeleton consists of SMA springs, arm orthoses, wearable fabrics, and rubber bands, as shown in Fig. 1.
- a.
SMA actuator. The strain of SMA wire is relatively low (less than 8 %), which cannot meet the movement requirements of the exoskeleton. In this paper, SMA springs are selected as the material of the SMA actuator. SMA springs have the advantages of large contraction, high energy density, large strain, and self-sensing, and can generate more than 200 % strain (Hadi et al., 2010). This characteristic of large deformation makes SMA springs a potential material for human bionic muscles. Based on previous studies (Xie et al., 2023, 2021), a NiTi SMA spring is selected in this paper (initial length λ0 is 20 mm, coil diameter D is 4.1 mm, wire diameter dS is 0.5 mm, and number of cycles N is 22). The contraction of a SMA spring after heating can produce a tensile force of more than 10 N, and the optimal pre-tensile length is 85–100 mm.
- b.
Wearing design of the exoskeleton. The SMA actuator is embedded in a soft fabric and worn on the elbow, as shown in Fig. 1a. The soft fabric is elastic and comfortable to wear, and it can adapt to the muscle changes caused by the contraction and relaxation of elbow flexor and extensor muscles. However, the deformation of the fabric will consume the output displacement and force of SMA actuator and reduce the actuating effect of the elbow. Therefore, orthoses with greater stiffness are installed on the arm (upper arm and forearm). The orthoses are made of low-temperature thermoplastic materials, and its stiffness is greater than that of fabric, which can produce less deformation and is suitable for exoskeleton fixation. Both ends of the elbow fabric are attached to the orthoses using rubber bands.
- c.
The design of antagonist muscle. A long rubber band is designed on the opposite side of the SMA actuator as the elbow extensor. When the SMA actuator is contracted, it drives the elbow to flex, and the long rubber band is extended to cooperate with it and provide a certain damping to achieve compliant motion, as shown in Fig. 1b. When the SMA actuator stops heating and the energy storage of the long rubber band reaches the maximum, the rubber band can provide a rebound force to make the SMA actuator return to the initial state and speed up the cooling rate of the SMA springs.
- d.
SMA heating and cooling method. SMA springs are heated by electricity, and the voltage of each group of springs is 5 V. A small fan is installed on the upper arm for SMA cooling. The SMA hybrid cooling method in this paper combines the resilience of the long rubber band, air cooling, and arm gravity.
2.2 Static analysis of human-exoskeleton coupling model
2.2.1 Static analysis of elbow flexion in different planes
Since the forearm can be rotated, the flexion/extension of the elbow has different motion planes. When the arm is in an upright position, the flexion/extension of the elbow is performed in the sagittal plane. When the forearm is pronated, the elbow flexion/extension is performed in a horizontal plane. In the sagittal plane, the elbow flexion movement is shown in Fig. 2a. At this time, the whole system is subjected to the active force including the force FSMA of the SMA actuator and the force Fmuscle of the elbow flexor, and the passive force including the combined gravity G1 of the forearm and hand, the object weight G2, and the pulling force Frubberband of the rubber bands. The static analysis in the sagittal plane is given by
In the horizontal plane, the elbow flexion movement is shown in Fig. 2b. At this time, the whole system is subjected to the active force including the force FSMA of the SMA actuator and the force Fmuscle of the elbow flexor, and the passive force including the pulling force Frubberband and the friction force f of the elbow joint. The static analysis in the horizontal plane is given by
Equation (1) minus Eq. (2) is obtained as follows:
, so τSMA1>τSMA2. Therefore, the required force FSMA of the SMA actuator in the sagittal plane is greater than that in the horizontal plane; that is, the assistance effect of the SMA actuator in the horizontal plane is better because the arm gravity effect in the horizontal plane is smaller. Thus, the flexion/extension of the elbow in the sagittal plane is discussed in the following part of this paper.
2.2.2 Design of bionic primary and antagonistic muscles (SMA springs and rubber bands)
The SMA spring in this paper is a one-way type; that is, the SMA spring needs to be stretched to a certain length (pre-stretched length) with the help of external force when it is at its original length (shortest length). After powering on, the SMA spring can be contracted to its original length, and the SMA spring can generate driving force and displacement during this contraction process. The driving force of the SMA spring is proportional to the pre-stretched length, as shown in Eq. (4) (Jeong et al., 2019). Within a certain range, the longer the pre-stretched length, the greater the driving force of the SMA spring. The experimental results of the relationship between driving force and pre-stretched length of SMA springs are shown in Fig. 3a based on previous studies (Xie et al., 2023). One SMA spring can produce a tensile force exceeding 10 N, and the optimal pre-tensile length is 85–100 mm. Overstretching SMA springs will reduce their fatigue lifetime. Since the tensile length of SMA springs cannot meet the needs of the elbow joint, two SMA springs are selected in series to increase their length.
where F is the force generated by the SMA spring, G is the shear modulus, dS is the wire diameter, λ is the displacement of the spring, D is the coil diameter, and N is the number of cycles of the SMA spring.
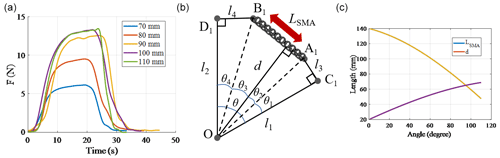
Figure 3Contraction force test and torque calculation of SMA springs. (a) The experimental results of the relationship between contraction force and pre-stretched length of SMA springs. (b) The geometric relationship between SMA springs and a human arm. (c) d and LSMA changing with the movement angle of elbow.
The geometric relationship between the SMA spring and human arm is shown in Fig. 3b. O is the virtual rotation center of the elbow joint. In analyzing the motion of the upper limb, the upper limb is often simplified as a rigid body model, in which the flexion and extension of the elbow joint are simplified as a revolute pair fixed by a revolute center (Bertomeu-Motos et al., 2018). A1 and B1 are the attachment points of the SMA spring to the forearm and upper arm, respectively. C1 and D1 are the bone positions corresponding to A1 and B1, respectively. l1 and l2 are the distances from C1 and D1 to O, and l3 and l4 are half the arm thicknesses at the attachment points of the upper arm and forearm; that is, the distances from A1 to C1 and B1 to D1. l3 and l4 are slightly different for different people. l1 and l2 are only concerned with the attachment points of SMA springs. Compared with l1 and l2, l3 and l4 are generally smaller, so they have less influence on the calculation of the angle of the elbow movement. LSMA is the length of the SMA spring, which changes during heating. d is the distance from LSMA to O. The supplementary angle of θ (180−θ) is the elbow joint movement angle, and θ1, θ2, θ3, and θ4 are included angles. According to geometry,
According to Eq. (5), if θ, l1, l2, l3, and l4 are known, d and LSMA can be solved. As shown in Fig. 3c, the curve of d and LSMA changing with the movement angle of the elbow joint is shown.
In this paper, the material of the bionic antagonistic muscle of the elbow joint is a rubber band. Rubber band is a general term for high-elastic polymer compounds. It shows elastic deformation under external loads and can be stretched up to 700 % or more. After unloading, it can be restored to its original shape and has excellent high elasticity, flexibility, fatigue resistance, and wear resistance. For the bionic antagonist of elbow flexion, rubber bands with a diameter of 50 mm, a thickness of 1.4 mm, and a width of 3 mm were selected, and long rubber bands were formed in series and parallel mode, as shown in Fig. 4a. During elbow flexion, the rubber band, which acts as the elbow extensor, is lengthened by the rotation center of the joint. Therefore, it is necessary to determine the elongation of the rubber band during elbow flexion. Stick one marker on the outside of your upper arm and forearm. The distance of the two markers at the neutral position and flexion to 120∘ of the elbow joint was measured. After repeated experiments, the average value was taken, and the distance difference between the measured flexion to 120∘ and the neutral position was 50–60 mm. For different measurement objects, the results were different, and the test results in this paper are for reference only.
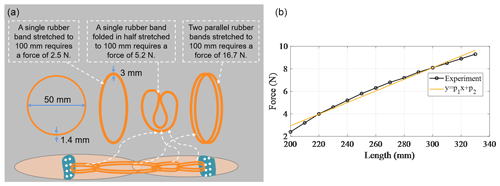
Figure 4The design of the bionic antagonistic muscles of the elbow joint. (a) The design of the bionic antagonistic muscle. (b) The tensile test results.
A single rubber band is characterized by a large stretch range and small tension. A single rubber band folded in half is characterized by a small stretch range and large tension. The stretching range and tension of two parallel rubber bands are between the first two, and this result is verified by tensile test experiments. When stretched to the same length (100 mm), a single rubber band pulls about 2.5 N, a single rubber band folded in half pulls about 5.2 N, and two parallel rubber bands pull about 16.7 N. To sum up, the bionic antagonistic muscle of elbow flexion is composed of three rubber bands folded in half and two parallel rubber bands in series. The tensile test results are shown in Fig. 4b. The experimental results can be approximately fitted to a linear equation, where p1=0.0516, , and the residual modulus is 0.9147. And two parallel rubber bands are designed at the joint, allowing for a wider stretch range that is more in line with elbow movement. When the elbow joint is flexed from the neutral position to 120∘, the length of the bionic antagonist muscle varies from 240–300 mm, the tension range is 5–8 N, and the torque is about 0.26–0.42 N m (the tension multiplied by the arm of force). The elbow flexed from the neutral position to 120∘, the position of the center of gravity, and the weight of the forearm can be obtained from the biomechanical parameters of the human body, and the torques of G1 and G2 can be predicted by multiplying its gravity by the arm of force. The sum of the torques of G1, G2 and rubber bands is the required torques for elbow motion. When a subject flexed the elbow joint from 0 to 120∘ with no load (G2=0), the sum of the torques of G1, G2, and rubber bands was divided by d to calculate the force required for elbow motion, which was the sum of forces of the muscle and SMA. When the subject's height and weight (1.72 m, 67 kg) and length parameters (l1=85 mm, l2=85 mm, l3=25 mm, l4=25 mm) are provided, the force required for elbow motion is calculated, and the SMA contraction force is equal to the force required for elbow motion when the subject is performing passive motion (the muscle force is zero), as shown in Fig. 5. The maximum force is 50 N when the elbow joint is flexed at an angle of 67∘. A force greater than 10 N can be generated when one SMA spring is stretched to a length of 85 mm, so the SMA combination of two series and four parallel groups is chosen in this paper. For different wearers, the contraction force of SMA can be calculated, and then the SMA combination that meets the requirements can be selected.
3.1 Experimental prototype and control method
The experimental prototype of the elbow exoskeleton is shown in Fig. 6. The SMA actuator was fixed on the soft fabric, and one end of the SMA spring was fixed on the heating module and the other end was connected by a wire, as shown in Fig. 6c and d. The exoskeleton was fixed with orthoses and straps, and the orthoses of the upper arm and forearm were connected to the fabric textile by rubber bands, as shown in Fig. 6a. The orthoses of the forearm and upper limb were connected by long rubber bands as the bionic antagonists of the exoskeleton, as shown in Fig. 6b. The wearable part of the elbow flexible exoskeleton prototype weighs only 230 g, including orthoses, SMA springs, rubber bands, fabric textile, and SMA heating modules, as shown in Fig. 6 below. The overall weight of the exoskeleton is 877 g.
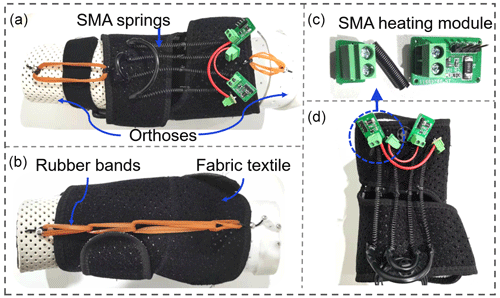
Figure 6Experimental prototype of elbow exoskeleton. (a, b) Experimental prototype. (c, d) SMA actuator and heating module.
It is known from the characteristics of SMA that the driving force and deformation are generated by the phase transformation of SMA springs through heating. By controlling the displacement of contraction and extension of SMA springs, the movement angle of the elbow joint can be controlled. At present, the main heating methods of SMA are pulse coding modulation (PCM) and pulse width modulation (PWM), in which PWM control is simple and effective and becomes the most important control technology of SMA electric heating. When the PWM pulse is at high current level, the SMA is in the heating state. When the PWM is at a low power level, the SMA stops heating. During the heating process of SMA, if its internal temperature is higher than the austenite start temperature (As), it begins to shrink. If the temperature is higher than the austenite finish temperature (Af), it reaches the complete shrinkage state. If the SMA continues to be heated, the internal temperature will continue to rise, causing the SMA temperature to be too high. When the temperature exceeds a certain threshold, it will cause damage to the SMA heating module and increase the risk of using the exoskeleton. Therefore, when the heating temperature of the SMA reaches Af, it is necessary to stop heating or maintain a constant temperature.
To realize the accurate control of the SMA actuator and elbow movement, the acquisition circuit including the SMA heating circuit, temperature, and angle signal was constructed. The control system includes an STM32F407 controller, SMA drive circuit, air cooling, elbow exoskeleton and sensors, as shown in Fig. 7, which constitute a complete execution and control system. The working principle of the control system is to input the desired SMA temperature and elbow motion angle into the controller, and the control module heats SMA springs according to the pre-set values. The temperature sensor and angle sensor feed back the data to the controller, the error value is compared with the pre-set value, and the input voltage of SMA springs is adjusted by controlling the duty cycle of PWM signals, so as to finally realize the motion control of elbow exoskeleton. The SMA drive circuit is used to heat SMA springs and control the spring contraction movements. The PWM is the control signal input. The drive circuit adopts an N-channel metallic oxide semiconductor (MOS) field-effect transistor A03400A, the maximum current is 5.7 A, and the MOS field-effect transistor is activated by the PWM signal to drive the SMA springs. The controller, STM32F407, is a high-performance 32-bit microcontroller (MCU) based on the Cortex-M4 core, with multiple timers that can be used to generate PWM output. The PWM generator has 1–3 channels of PWM output, a frequency adjustment range of 1–150 KHz, uses serial communication, and each PWM duty cycle can be adjusted independently. The temperature sensor, the infrared temperature measurement module GY-906, adopts a non-contact temperature measurement method, the temperature measurement accuracy can reach 0.02 ∘C, and the range is −70 to 382.2 ∘C, which can meet the temperature measurement needs of SMA. The angle sensor is an ATK-IMU901 angle sensor module that integrates a gyroscope (3D), accelerometer (3D), magnetometer (3D), and barometer (1D). It uses a 32-bit 72 MHz processor to quickly solve the real-time motion attitude of the module. The static X\Y axis measurement accuracy of the module is 0.05∘. For air cooling, the speed of the micro DC cooling fan is 7500 r min−1 and the working voltage is 5 V.
3.2 PWM experiment
PWM is used as the input of the SMA control signal, and the heating rate of the SMA spring can be controlled by adjusting the duty cycle. Selecting the appropriate voltage, current, and duty cycle is beneficial to improve the driving efficiency of the SMA. The experimental setup of PWM is shown in Fig. 8. The experimental object is a set of SMA springs (four in series) of the elbow exoskeleton. The PWM experiment was carried out at room temperature of 22 ∘C. As can be seen from Fig. 8, the temperature sensor measured the temperature of the initial segment of SMA. The initial segment of SMA was connected to the SMA drive circuit. The SMA did not heat up equally along its entire length, and the temperature of the initial segment was higher than other locations. Thus, the initial segment was selected to measure the temperature of SMA, which will avoid localized high temperatures, and a small fan was installed next to the temperature sensor.
The heating speed of SMA can be accelerated by selecting an appropriate voltage and duty cycle, so the temperature change of the SMA spring under different voltages and duty cycles was tested in this paper. The experimental voltage range was 10–13 V and the current was 2.2 A. The experimental results are shown in Fig. 9a. According to the experimental results, the higher the voltage, the faster the heating rate, and the heating rate of each curve changes from slow to fast, which is the result of rapid heating after heat accumulation. Therefore, choosing a larger voltage can speed up the heating rate of the SMA.
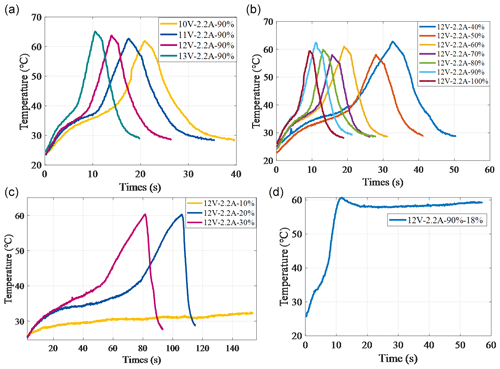
Figure 9The temperature change of the SMA spring (a) under different voltages, (b, c) under different duty cycles, and (d) when maintaining a constant temperature.
The temperature change of the SMA spring was tested under different duty cycles. The voltage was 12 V and the current was 2.2 A. The experimental results are shown in Fig. 9b. According to the experimental results, the higher the duty cycle is, the faster the heating rate is, and the heating rate of each curve changes from slow to fast. From a 40 % duty cycle to 100 %, the warming amplitude decreases, and the heating rate of the duty cycle 90 % is very close to that of duty cycle 100 %. Therefore, selecting a duty cycle of more than 90 % can speed up the heating rate of SMA.
When the heating temperature of SMA reaches Af, it is necessary to stop heating or maintain a constant temperature. Therefore, to determine the duty cycle of SMA insulation, the temperature change of the SMA spring under a small duty cycle was tested. The voltage was 12 V and the current was 2.2 A. The experimental results are shown in Fig. 9c. According to the experimental results, when the duty cycle is 30 % and 20 %, the SMA spring is still in a heating state; when the duty cycle is 10 %, the heating rate is close to zero. Thus, the duty cycle for maintaining a constant temperature is between 10 % and 20 %.
The duty cycle of the SMA spring to maintain a constant temperature was tested. The operating temperature of SMA spring was 60 ∘C, the voltage was 12 V, and the current was 2.2 A. As the duty cycle of SMA heating, 90 % was selected and the heating effect was tested with a duty cycle of 10 % to 20 %. Finally, 18 % was selected as the duty cycle of SMA to maintain a constant temperature. The experimental results are shown in Fig. 9d. After the duty cycle is 90 % and heated to 60 ∘C, it is switched to a small duty cycle of 18 %, and the SMA temperature can be maintained at about 60 ∘C. At this point, the SMA spring remains fully retracted, which can output the maximum force and displacement, and the elbow exoskeleton is in the maximum flexion position.
3.3 Experiment of elbow joint angle and SMA temperature
To verify the training effect of the SMA-driven flexible elbow exoskeleton, a healthy subject (female, height of 1.72 m, weight of 67 kg) was selected to test the changes of the elbow joint angle and SMA temperature. The flexible elbow exoskeleton was easy to wear and took less than 2 min. The orthoses on the upper arm and forearm are fastened with straps on the arm, which are easy to put on and take off. During the test, the subject's arm was in a relaxed state without load (G2=0), and the SMA actuator was heated with electricity (voltage of 12 V, current of 2.2 A, and the PWM duty cycle was 90 % during heating). When the temperature of the SMA was heated to As, the SMA actuator contracted to drive the elbow joint to flex. When the temperature of the SMA was heated to Af, the air cooling was turned on after the power was cut off, and the elbow joint was extended to the neutral position under arm gravity and rubber band action. An angle sensor (ATK-IMU901) was installed on the forearm to record the motion angle of the elbow joint, and an infrared temperature sensor (GY-906) was installed at the SMA actuator to collect temperature data during the experiment, as shown in Fig. 10. During the cyclic flexion/extension movement of the elbow joint, the maximum angle of elbow flexion is about 80∘, and the maximum temperature is about 60–70 ∘C, which can be maintained in the SMA operating temperature range without high temperature.
Over the past decade, SMA materials have been successfully used in a variety of applications, from the biomedical field to robotics and automation (Kim et al., 2019). Skeletal muscles are the power components of human limb movement, which has the advantages of quick response, high force-weight ratio, flexibility, and coordination, etc. It combines the contraction and relaxation of the primary and antagonistic muscles to complete the coupling driving function of biological joints. SMA is a kind of active deformation material with a self-sensing and driving ability. And SMA actuators are ideal alternatives to pneumatic, hydraulic, or motor drives due to their high power–weight ratio, simple structure, light weight, and small size; they are very similar to the performance of human muscles. However, the existing flexible exoskeletons driven by SMA are only designed with bionic primary muscles, ignoring the role of antagonistic muscles. The coordination of antagonistic muscles is essential for the primary muscles to complete joint movements, and the timely contraction of antagonistic muscles is also an important guarantee for accurate and compliant movement. This paper proposes a soft bionic elbow exoskeleton based on SMA spring actuators (which can be practical at home with one power unit), which can be used for assisting elbow movement. The elbow exoskeleton combines an active deformation material (SMA) with a highly elastic material (rubber band) to simulate the contraction and relaxation of the skeletal muscles of the elbow joint. When the SMA actuator contracts and actuates the elbow joint to flex, the rubber band stretches to cooperate with it, which can provide a certain damping and achieve a compliant movement. And the rubber band also provides resilience to restore the SMA actuator to its original state, enabling elbow flexion and extension.
Portability. The portability and comfort of the flexible exoskeleton can effectively improve the utilization rate, and the light-weight structure can effectively reduce the user's energy consumption. This paper proposes a SMA-driven light-weight flexible elbow exoskeleton, Sobee-SMA, which is made of flexible materials and its wearable part weighs 230 g. It can be used at home, overcoming the problem of poor wearable comfort and portability of a rigid elbow exoskeleton (Vitiello et al., 2012, 2016).
Bionics. The bionics of the exoskeleton is to simulate the motion of human joints and conform to human motion to reduce human–exoskeleton interference. Park et al. (2020) and Park and Park (2019) proposed a flexible upper limb exosuit, the actuator of which is a series-parallel combination of 20 SMA springs. The SMA actuator can generate a force of over 100 N after heating, but it only simulates the primary muscle of elbow flexion and lacks antagonistic muscle. The Sobee-SMA exoskeleton in this paper uses SMA actuators and rubber bands to simulate the primary and antagonist muscles of elbow flexion. When the SMA actuator is contracted, it drives the elbow joint to flex, and the rubber band stretches to cooperate with it, which can provide a certain damping, realize the compliant movement of the joint, and provide a rebound force to make the SMA actuator return to the initial state.
SMA cooling method. Jeong et al. (2019, 2021) developed a flexible upper limb exoskeleton with active SMA cooling. The cooling method is to cool the SMA spring through cooling liquid circulation in a stretchable coolant vessel, and the frequency of driving the flexion and extension of the wrist is 0.1 Hz. This method greatly increases the driving efficiency of the SMA actuator but requires consideration of coolant leakage. The Sobee-SMA exoskeleton in this paper adopts a hybrid cooling method that combines the elastic force of rubber bands, air cooling, and arm gravity. This cooling method is not as efficient in driving as coolant, but it is easier to control and does not require the consideration of coolant leakage.
Assisting effect. According to the experiment of the elbow joint angle and SMA temperature, the motion angle of the elbow of the subject is about 0–80 ∘C, and the maximum temperature range is about 60–70 ∘C. The maximum temperature can be maintained at the operating temperature of the SMA spring without excessive temperature. However, the normal range of motion (ROM) of the elbow is 0–120 ∘C, and the ROM of Sobee-SMA only reaches 66.7 % of normal ROM. The ROM of Sobee-SMA needs to be further improved in the follow-up work.
Limitations. The assisting effect and driving frequency of Sobee-SMA should be further improved in the follow-up work. New SMA actuators will be designed to increase the output of displacement, and more efficient SMA heating and cooling methods will be studied to improve the efficiency of the SMA actuators.
The combination of SMA and wearable robotic technology has the advantages of being light weight, energy-saving, and having great human–exoskeleton interaction. We proposed and designed a novel soft exoskeleton (Sobee-SMA) based on SMA spring actuators for assisting elbow flexion and extension movements. The following new elements were developed for the Sobee-SMA:
-
Skeletal muscles combine the contraction and relaxation of the primary muscles and antagonistic muscles to complete the coupling driving function of biological joints. The primary muscle provides the driving force, and the antagonistic muscle acts as a damping to make joint motion more accurate and compliant. The existing flexible elbow exoskeletons actuated by SMA materials are only designed with bionic primary muscles, ignoring the role of antagonistic muscles. This paper presents the elbow exoskeleton based on SMA springs, which adopts a bionic design and combines an active deformation material (SMA) with a highly elastic material (rubber band) to simulate the contraction and relaxation of elbow skeletal muscles. When the SMA actuator contracts and actuates the elbow joint to flex, the rubber band stretches to cooperate with it, which can provide a certain damping and achieve a compliant movement. And the rubber band also provides resilience to restore the SMA actuator to its original state, enabling elbow flexion and extension.
-
Through the PWM experiment, we can obtain the duty ratio of the SMA-energized heating to maintain a constant temperature state, so that the SMA spring can be kept at the temperature of the maximum deformation state, which can reduce the risk of SMA temperature heating too high and damaging the skin.
To investigate the effects of assistance with the elbow motions produced by the Sobee-SMA, user tests were conducted with a healthy subject. Through the PWM experiment, the driving voltage is selected as 12 V, the PWM duty cycle is 90 % during heating, and the PWM duty cycle is 18 % during heat preservation. In the relaxed state of healthy subjects, the range of motion of the elbow is about 0–80∘, and the maximum temperature is about 60–70 ∘C. However, the ROM of the elbow is 0–120∘, and the ROM of Sobee-SMA only reaches 66.7 % of the ROM. In the future, we will continue to research SMA actuators and improve the assisting effect and driving frequency of the elbow exoskeleton in follow-up work.
All data included in this study are available upon request from the corresponding author.
QX conceived the idea, developed the method, and wrote the majority of the paper. QM, WY, and HY supervised and structured the paper. RX and XW performed experiments. XW edited the paper.
The contact author has declared that none of the authors has any competing interests.
Publisher's note: Copernicus Publications remains neutral with regard to jurisdictional claims in published maps and institutional affiliations.
The authors would also like to thank Ting Ai, Qingxin Zeng, and Zongqi Jiao for their help with the writing and experiments.
The authors have been supported financially by the National Key R&D Program of China (2022YFC3601103), National Natural Science Foundation of China (61803265), Shanghai Foundation for Development and Technology, China (grant no. 20S31905400), and the program of China Scholarships Council (grant no. 202208310171).
This paper was edited by Zi Bin and reviewed by two anonymous referees.
Ang, B. W. K. and Yeow, C. H.: Design and Modeling of a High Force Soft Actuator for Assisted Elbow Flexion, IEEE Robotics and Automation Letters, 5, 3731–3736, https://doi.org/10.1109/LRA.2020.2980990, 2020.
Bertomeu-Motos, A., Blanco, A., Badesa, F. J., Barios, J. A., Zollo, L., and Garcia-Aracil, N.: Human arm joints reconstruction algorithm in rehabilitation therapies assisted by end-effector robotic devices, J. Neuroeng. Rehabil., 15, 1–11, https://doi.org/10.1186/s12984-018-0348-0, 2018.
Copaci, D., Blanco, D., and Moreno, L. E.: Flexible shape-memory alloy-based actuator: Mechanical design optimization according to application, Actuators, 8, 63, https://doi.org/10.3390/act8030063, 2019.
Copaci, D.-S., Blanco, D., Martin-Clemente, A., and Moreno, L.: Flexible shape memory alloy actuators for soft robotics: Modelling and control, Int. J. Adv. Robot. Syst., 17, 1729881419886747, https://doi.org/10.1177/1729881419886747, 2020.
Dinh, B. K., Xiloyannis, M., Cappello, L., Antuvan, C. W., Yen, S.-C., and Masia, L.: Adaptive backlash compensation in upper limb soft wearable exoskeletons, Robot. Auton. Syst., 92, 173–186, https://doi.org/10.1016/j.robot.2017.03.012, 2017.
Hadi, A., Yousefi-Koma, A., Moghaddam, M. M., Elahinia, M., and Ghazavi, A.: Developing a novel SMA-actuated robotic module, Sensor. Actuat. A-Phys., 162, 72–81, https://doi.org/10.1016/j.sna.2010.06.014, 2010.
Jeong, J., Yasir, I. B., Han, J., Park, C. H., Bok, S.-K., and Kyung, K.-U.: Design of shape memory alloy-based soft wearable robot for assisting wrist motion, Appl. Sci.-Basel, 9, 4025, https://doi.org/10.3390/app9194025, 2019.
Jeong, J., Hyeon, K., Han, J., Park, C. H., Ahn, S.-Y., Bok, S.-K., and Kyung, K.-U.: Wrist assisting soft wearable robot with stretchable coolant vessel integrated SMA muscle, IEEE-ASME T. Mech., 27, 1046–1058, https://doi.org/10.1109/TMECH.2021.3078472, 2021.
Jeong, J., Hyeon, K., Jang, S. Y., Chung, C. Y., Hussain, S., Ahn, S. Y., Bok, S. K., and Kyung, K. U.: Soft Wearable Robot With Shape Memory Alloy (SMA)-Based Artificial Muscle for Assisting With Elbow Flexion and Forearm Supination/Pronation, IEEE Robotics and Automation Letters, 7, 6028–6035, 2022.
Kim, Y., Jang, T., Gurung, H., Mansour, N. A., Ryu, B., and Shin, B.: Bidirectional rotating actuators using shape memory alloy wires, Sensor. Actuat. A-Phys., 295, 512–522, https://doi.org/10.1016/j.sna.2019.05.047, 2019.
Koh, T. H., Cheng, N., Yap, H. K., and Yeow, C.-H.: Design of a soft robotic elbow sleeve with passive and intent-controlled actuation, Frontiers in Neuroscience, 11, 597, https://doi.org/10.3389/fnins.2017.00597, 2017.
Kwakkel, G., Kollen, B. J., and Wagenaar, R. C.: Therapy impact on functional recovery in stroke rehabilitation: a critical review of the literature, Physiotherapy, 85, 377–391, https://doi.org/10.1016/S0031-9406(05)67198-2, 1999.
Lotti, N., Xiloyannis, M., Durandau, G., Galofaro, E., Sanguineti, V., Masia, L., and Sartori, M.: Adaptive model-based myoelectric control for a soft wearable arm exosuit: A new generation of wearable robot control, IEEE Robot. Autom. Mag., 27, 43–53, https://doi.org/10.1109/MRA.2019.2955669, 2020.
Park, S. J. and Park, C. H.: Suit-type Wearable Robot Powered by Shape-memory-alloy-based Fabric Muscle, Sci. Rep.-UK, 9, 9157, https://doi.org/10.1038/s41598-019-45722-x, 2019.
Park, S. J., Kim, U., and Park, C. H.: A novel fabric muscle based on shape memory alloy springs, Soft Robot., 7, 321–331, https://doi.org/10.1089/soro.2018.0107, 2020.
Pérez Vidal, A. F., Rumbo Morales, J. Y., Ortiz Torres, G., Sorcia Vázquez, F. d. J., Cruz Rojas, A., Brizuela Mendoza, J. A., and Rodríguez Cerda, J. C.: Soft Exoskeletons: Development, Requirements, and Challenges of the Last Decade, Actuators, 10, 166, https://doi.org/10.3390/act10070166, 2021.
Villoslada, A., Flores, A., Copaci, D., Blanco, D., and Moreno, L.: High-displacement flexible shape memory alloy actuator for soft wearable robots, Robot. Auton. Syst., 73, 91–101, https://doi.org/10.1016/j.robot.2014.09.026, 2015.
Vitiello, N., Lenzi, T., Roccella, S., De Rossi, S. M. M., Cattin, E., Giovacchini, F., Vecchi, F., and Carrozza, M. C.: NEUROExos: A powered elbow exoskeleton for physical rehabilitation, IEEE T. Robot., 29, 220–235, https://doi.org/10.1109/TRO.2012.2211492, 2012.
Vitiello, N., Cempini, M., Crea, S., Giovacchini, F., Cortese, M., Moise, M., Posteraro, F., and Carrozza, M. C.: Functional design of a powered elbow orthosis toward its clinical employment, IEEE-ASME T. Mech., 21, 1880–1891, https://doi.org/10.1109/TMECH.2016.2558646, 2016.
Xie, Q., Meng, Q., Zeng, Q., Dai, Y., Wu, Z., Chen, L., and Yu, H.: Design of a Soft Wrist Exoskeleton Based on SMA Actuator Module SMA, Jiqiren/Robot, 43, 406–413, https://doi.org/10.13973/j.cnki.robot.200584, 2021.
Xie, Q., Meng, Q., Yu, W., Wu, Z., Xu, R., Zeng, Q., Zhou, Z., Yang, T., and Yu, H.: Design of a SMA-based soft composite structure for wearable rehabilitation gloves, Frontiers in Neurorobotics, 17, 1047493, https://doi.org/10.3389/fnbot.2023.1047493, 2023.
Xiloyannis, M., Annese, E., Canesi, M., Kodiyan, A., Bicchi, A., Micera, S., Ajoudani, A., and Masia, L.: Design and validation of a modular one-to-many actuator for a soft wearable exosuit, Frontiers in Neurorobotics, 13, 39, https://doi.org/10.3389/fnbot.2019.00039, 2019a.
Xiloyannis, M., Chiaradia, D., Frisoli, A., and Masia, L.: Physiological and kinematic effects of a soft exosuit on arm movements, J. Neuroeng. Rehabil., 16, 29, https://doi.org/10.1186/s12984-019-0495-y, 2019b.
Xiloyannis, M., Alicea, R., Georgarakis, A.-M., Haufe, F. L., Wolf, P., Masia, L., and Riener, R.: Soft robotic suits: State of the art, core technologies, and open challenges, IEEE T. Robot., 38, 1343–1362, https://doi.org/10.1109/TRO.2021.3084466, 2021.
Xu, Q., Li, C., Pan, Y., Li, W., Jia, T., Li, Z., Ma, D., Pang, X., and Ji, L.: Impact of smart force feedback rehabilitation robot training on upper limb motor function in the subacute stage of stroke, Neurorehabilitation, 47, 209–215, https://doi.org/10.3233/NRE-203130, 2020.