the Creative Commons Attribution 4.0 License.
the Creative Commons Attribution 4.0 License.
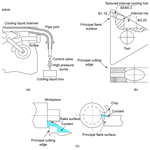
Short communication: Experiment study on micro-textured tool with internal cooling
Gang Yang
Wei Feng
Higher cutting force and its temperature with faster tool wear are the causes of higher production costs and lower machining efficiency. In this paper, with the help of electrical discharge machining (EDM) and laser technology, texture holes are implemented on the rake face and the principal flank face of the tool. The cutting force, friction characteristics of rake face and surface roughness of rake face are compared with the micro-textured cutting tool and the processing technology system of non-textured inner cooling hole. The results show that the coolant can be effectively sent to the interface surfaces due to the internal cooling texture cutter.
- Article
(871 KB) - Full-text XML
- BibTeX
- EndNote
Friction and wear are inevitable problems in machining. Previous researchers mainly started with materials, structures, lubricants, additives and surface coatings, and made the surface as smooth as possible. The latest research shows that the surface of the friction pair has a certain non-smooth shape but it has better anti-friction effects. At present, the surface texture is the focus of research; processing various textures and shapes on the surface of friction pairs can be beneficial to the infiltration, storage and film formation of lubricating media, thus, achieving better antifriction and anti-friction effects, prolonging the life of tools and reducing production costs (Liu et al., 2019). Currently, although there are also technologies such as cold air cutting, liquid nitrogen cooling cutting, water vapor cutting, etc. (Liu et al., 2005; Rajurkar and Wang, 2019), their main functions are cooling rather than lubrication. A better understanding of the chip formation mechanism plays a crucial role in machining process planning, surface integrity improvement and, thus, product performance (Guo and Yen, 2004; Pawade and Joshi, 2011). In recent years, with the deepening research of laser surface microtexture, Deng et al. (2012) have made microtexture self-lubricating tools with laser marking machines. The research found that the tool can not only reduce the contact length between the chip and the tool but also the solid lubricant in the groove can form a low shear strength lubricating oil film at the interface between the tool and the chip. Koshy and Tovey (2011) made two types of surface textures, continuous texture and groove array, on the rake face of high-speed steel tools and found that the texture can promote cutting fluid entry to the tool–chip friction interface. Niketh and Samuel (2018) studied the effect of micro-textures in enhancing the tribological characteristics of surfaces under dry sliding contact and its application on drill tools for reducing thrust and torque while machining Ti-6Al-4V alloy under dry, wet and MQL conditions. Li et al. (2017) compared the friction factors of three micro-texture tools (traditional tool, micro-groove tool and nano-texture tool) and the results demonstrated that the friction factors of micro-texture tools were reduced by 11.5 % and 10.9 %, respectively, compared with the other two tools. Yang et al. (2018) compared the tribological properties of several different micro-textures. The results show that the friction coefficient and friction volume of micro-pit texture surface is the smallest when it rubs against titanium alloy. Wu et al. (2012) compared the tool wear of three micro-textures and the results showed that the life of the tool with the elliptical groove on the rake face and micro-groove parallel to the cutting edge increased by 10 %–15 % and 10 %–30 %, respectively. Sivaiah et al. (2020) studied the fabrication of new texture design tools and machinability evaluation of these developed tools in the turning of AISI 304 material under conventionally dry and cutting environment. Results indicated that the machinability of AISI 304 was significantly improved with the hybrid tools under conventional cooling compared to dry cutting conditions, respectively. According to the research of Rao et al. (2018), the rake face wear of the tool with micro-pits on both the rake face and the principal flank face is reduced by 62 %–40 % compared with the traditional tool and the tool with micro-pits on the rake face. A better understanding of chip formation mechanism plays an important role in machining process planning, surface integrity improvement and, thus, product performance. In consideration of its significance, much research on chip formation mechanism under different cutting conditions is indispensable to a deep insight into the whole cutting process (Wang and Liu, 2012). However, while the micro-texture treatment of the tool can improve the lubrication and cutting effect, its maintenance time is relatively limited. Under the conditions of high temperature, high pressure and severe friction, the micro-texture hole or groove will be filled with chips quickly and lose its function. Besides this, the effect of micro-texture is not ideal under heavy load rough machining and most micro-texture areas are concentrated in the rake face.
The purpose of this study is to use electrical discharge machining (EDM) and femtosecond laser technology, while the texture with a larger aperture is made on the rake face of the tool, which is connected with the internal cooling hole, so as to achieve the functions of cooling, lubricating, reducing friction and changing chip state. At the same time, in this study, coolant holes were created on the main flank of the tool to face the transition surface which further reduced the cutting temperature and reduced the friction between the tool and chips.
2.1 Experiment setup
The experimental object is 0Gr18Ni9 (ASTM AISI, 304) which is austenitic stainless steel. It is widely used as heat-resistant steel including in food equipment, general chemical equipment, atomic energy industry equipment, etc. The material has high ductility, high impact toughness and low thermal conductivity so it consumes more power during cutting, and the cutting head is not easy to disperse, the cutting temperature is high and the hardening during machining is serious. Therefore, TNMG160404-SG XL7020 of JCCSG Company (belonging to the YW class of common brands in China) is selected for turning tools.
The schematic of the apparatus is constructed with the following steps: firstly, the turning tool is modified by EDM machine tool and two main holes of the inner coolant are machined (∅ 3.25, holes are connected with the coolant passage hole of the tool body and ∅ 1.15 is a through hole which penetrates to the main flank of the tool as shown in Fig. 1a and b. Then, texture treatment is carried out on the wear area of the rake face of the turning tool by laser equipment and texture holes are machined.
There are eight textured internal cooling holes in three rows with a diameter of ∅ 0.3 mm in which the center of the hole in the first row is 0.7 mm away from the main cutting edge and 1 mm away from the tool tip, and the center distance between the rows and columns is 0.4 mm which runs through the ∅ 1.15 inner cooling liquid main hole. The texture size of the rake face of the machining tool is shown in Fig. 1. The turning tool body is reformed and a coolant hole communicated with the main coolant hole in the turning tool is machined. Finally, the textured tool on the cutter body is installed and connected to the corresponding coolant tank, high-pressure water pump, control valve and coolant channel to form an internal cooling circulation system. Figure 1c shows the photo after the coolant is sprayed out.
2.2 Mechanism
The coolant enters the interface between the tool and the chip face for cooling and lubrication. Then the coolant begins to form a lubricating oil film between the tool and the chip face during continuous machining which plays a role in reducing friction and lubrication. At the same time, due to the pressure of the cooling liquid, the chip shape changes.
3.1 Cutting force and average friction coefficient
In CDL6136 lathe, the turning tool is connected to YDC-89A piezoelectric turning dynamometer developed by Dalian University of Technology. The cutting experimental parameters are as follows: back cutting amount ap=1 mm, feed rate f=0.2 mm r−1, continuous cutting time 5 min and taking the average value of three-dimensional cutting forces of two kinds of cutting tools varying with cutting speed.
It can be seen from Fig. 2 that the main cutting force, the feed force, the back force and the cutting force are reduced by 2 %–5 %, 8 %–24 %, 2 %–7.5 % and 1 %–8 %, respectively. Among them, the feed force decreased obviously. However, the friction coefficient between cutter and chip surface also decreases by 2 %–8.6 % with the increase of cutting speed. It can be seen from Fig. 2c that the friction coefficient only decreases by 0.1 when the cutting speed is in the range of 70–90 but decreases by 0.4 when the cutting speed reaches 100, which shows that the friction coefficient decreases more obviously when the cutting speed is higher. It is obvious that the cooling holes in the texture play a better role in reducing cutting force and friction.
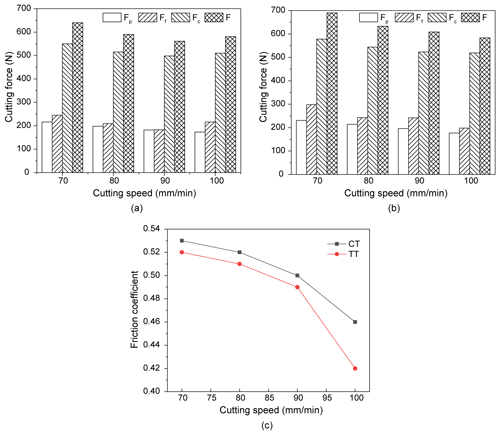
Figure 2Effect of cutting speed of CTs (conventional tools) and TTs (micro-textured tools) on cutting force and average friction coefficient: (a) CT cutter cutting force with cutting speed, (b) TT cutter cutting force with cutting speed and (c) cutter-chip interface friction coefficient with cutting speed.
3.2 Surface roughness measurement
Using TR200 roughness meter, the surface roughness of five samples processed respectively were measured and the measurement parameters were as follows: sampling length 0.8 mm, evaluation length and measuring range. The roughness of TT tool is reduced by 24.7 % compared with that of CT tool which shows that the cooling and lubrication effect of cooling holes in the texture is very satisfactory. This effectively reduces the chip accumulation tumor adhered to the cutting edge, the scaling and sticking of the machined surface and the wear of the main rake face. At the same time, because the coolant has a certain pressure, the chip outflow gets larger shear angle, the chip thickness compression ratio is reduced and the cutting deformation is small, thus, ensuring the surface machining quality.
3.3 Surface topography
After the test, a white light interference surface three-dimensional and two-dimensional profiler was utilized to compare and observe the change of microscopic characteristics of the friction surface of the tool, and the mechanism of anti-friction and anti-adhesion of the tool with internal cooling texture was analyzed. Figure 3 is a comparison of the wear morphology of the rake face of the CT tool after cutting for 4 min under the cutting conditions of , ap=1 mm, f=0.2 mm r−1. It can be seen from Fig. 3b that typical crescent-shaped dimple wear appears on the CT rake face and a large number of stickies are found under the condition. It is evident from Fig. 3 that the wear of the TT rake face is small. It shows that the effect of the cooling tool on texture is very good.
-
Electric spark and laser technology are used in this study. Internal cooling texture treatment was carried out on TNMG160404-SG XL7020 cemented carbide insert so that it can be internally cooled at the front edge and the main rear edge. Compared to the non-textured insert, it is reported that the textured insert can reduce the actual contact area between the insert and the chip, improve the friction state and have obvious effects on reducing cutting force (in which the feed force decreases obviously, by about 8 %–24 % and the cutting force decreases by 1 %–8 %), and the average friction coefficient of the interface between the tool and the chip decreases by about 2 %–8.6 %.
-
The wear of the front and back edges of the textured cutter is reduced which greatly improves the service life of the cutter. The use of internal cooling greatly reduces the amount of cutting fluid needed in continuous casting and external cooling mode, and can improve certain environmental protection requirements and waste liquid treatment costs.
All raw data can be provided by the corresponding authors upon request.
GY was responsible for the conceptualization, methodology, funding acquisition, resources, experimental guidance, experimental design, writing of the original draft, and review and editing. WF was responsible for writing the original draft, experiment, and data analysis.
The contact author has declared that neither of the authors has any competing interests.
Publisher’s note: Copernicus Publications remains neutral with regard to jurisdictional claims in published maps and institutional affiliations.
This paper was edited by Jeong Hoon Ko and reviewed by two anonymous referees.
Deng, J., Wu, Z., Lian, Y., Qi, T., and Cheng, J.: Performance of carbide tools with textured rake-face filled with solid lubricants in dry cutting processes, Int. J. Refract. Met. H., 30, 164–172, https://doi.org/10.1016/j.ijrmhm.2011.08.002, 2012.
Guo, Y. B. and Yen, D. W.: A FEM study on mechanisms of discontinuous chip formation in hard machining, J. Mater. Process. Tech., 155, 1350–1356, https://doi.org/10.1016/j.jmatprotec.2004.04.210, 2004.
Koshy, P. and Tovey, J.: Performance of electrical discharge textured cutting tools, CIRP Ann.-Manuf. Techn., 60, 153–156, https://doi.org/10.1016/j.cirp.2011.03.104, 2011.
Li, N., Chen, Y., Kong, D., and Tan, S.: Experimental investigation with respect to the performance of deep submillimeter-scaled textured tools in dry turning titanium alloy Ti-6Al-4V, Appl. Surf. Sci., 403, 187–199, https://doi.org/10.1016/j.apsusc.2017.01.166, 2017.
Liu, J., Han, R., and Sun, Y.: Research on experiments and action mechanism with water vapor as coolant and lubricant in Green cutting, Int. J. Mach. Tool Manu., 45, 687–694, https://doi.org/10.1016/j.ijmachtools.2004.09.022, 2005.
Liu, X., Liu, Y., Li, L., and Tian, Y.: Performances of micro-textured WC-10Ni3Al cemented carbides cutting tool in turning of Ti6Al4V, Int. J. Refract. Met. H., 84, 104987, https://doi.org/10.1016/j.ijrmhm.2019.104987, 2019.
Niketh, S. and Samuel, G. L.: Drilling performance of micro textured tools under dry, wet and MQL condition, J. Manuf. Process., 32, 254–268, https://doi.org/10.1016/j.jmapro.2018.02.012, 2018.
Pawade, R. S. and Joshi, S. S.: Mechanism of chip formation in high-speed turning of Inconel 718, Mach. Sci. Technol., 15, 132–152, https://doi.org/10.1080/10910344.2011.557974, 2011.
Rajurkar, K. P. and Wang, Z. Y.: Cryogenic machining of hard-to-cut materials, Wear, 239, 168–175, https://doi.org/10.1016/S0043-1648(99)00361-0, 2000.
Rao, C. M., Rao, S. S., and Herbert, M. A.: Development of novel cutting tool with a micro-hole pattern on PCD insert in machining of titanium alloy, J. Manuf. Process., 36, 93–103, https://doi.org/10.1016/j.jmapro.2018.09.028, 2018.
Sivaiah, P., Singh, M., Venkatesu, S., and Yoganjaneyulu, G.: Investigation on turning process performance using hybrid-textured tools under dry and conventional cooling environment, Mater. Manuf. Process., 35, 1852–1859, https://doi.org/10.1080/10426914.2020.1813893, 2020.
Wang, B. and Liu, Z.: Serrated chip formation mechanism based on mixed mode of ductile fracture and adiabatic shear, Proceedings of the Institution of Mechanical Engineers, P. I. Mech. Eng. B-J. Eng., 228, 181–190, https://doi.org/10.1177/0954405413497941, 2014.
Wu, Z., Deng, J., Chen, Y., Xing, Y., and Zhao, J.: Performance of the self-lubricating textured tools in dry cutting of Ti-6Al-4V, Int. J. Adv. Manu. Tech., 62, 943–951, https://doi.org/10.1007/s00170-011-3853-x, 2012.
Yang, S., Liu, W., Zhang, Y., and Wan, Q.: Experimental evaluation on micro-texture parameters of carbide ball-nosed end mill in machining of titanium alloy, Int. J. Adv. Manu. Tech., 96, 1579–1589, https://doi.org/10.1007/s00170-017-0659-5, 2018.