the Creative Commons Attribution 4.0 License.
the Creative Commons Attribution 4.0 License.
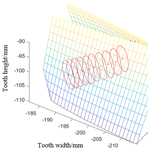
Ellipsoid contact analysis and application in the surface conjugate theory of face gears
Xiaomeng Chu
Yali Liu
Hong Zeng
The face gear tooth surface is a high-order variable curvature surface, and the curvature of the surface is complicated, so it is difficult to describe the characteristics of the face gear tooth surface by a specific equation. In this paper, the discrete curvature relation of the surface is used instead of an analytical equation to describe a spatial meshing surface, and the traditional meshing theory is neutralized to analyze the characteristics of the face gear tooth surface. Firstly, according to the structural characteristics of the face gear, the sampling method of the face gear tooth surface is analyzed, and the mathematical model of fitting the tooth surface contact point is established. Then, the discrete asymptotic surface development analysis method is studied, and the ellipsoid contact analysis method of the face gear pair is established by simplifying the conjugate surface and its region. Finally, the contact analysis method of the discrete tooth surface is studied, and the instantaneous contact ellipse of the face gear tooth surface is calculated, which formed a new numerical meshing method of space curved surface.
- Article
(2437 KB) - Full-text XML
- BibTeX
- EndNote
The gear is the symbol of industrialization. The face gear is an advanced new configuration gear. The face gear transmission is a new type of advanced transmission that meshes with a kind of cylindrical spur gear and bevel gear. Compared with the traditional spiral bevel gear drive, it has the advantages of compact structure, small size, lightweight, high bearing capacity, high reliability, good interchangeability, no axial force, and remarkable processing efficiency, which can improve the transmission power and lifetime.
Face gear transmission has broad application prospects in the field of intersecting shaft power and motion transmission because of its simple structure, low vibration and noise, insensitivity to installation error, power split, and high interchangeability. NASA has funded projects such as the Advanced Rotor Program and the Rotorcraft Transmission Research Program (RDS-21), which have successfully applied face gear transmission technology to the power split device of a helicopter main reducer, greatly improving the overall performance of the transmission system. The face gear transmission technology has been successfully applied to the automotive power transmission system. Audi has successfully applied the face gear technology to the central differential, which reduces the weight compared to the traditional transmission mode and increases the torque distribution ratio between the front and rear wheels. In addition, the contribution ratio between the front and rear wheels has been improved. In addition, face gear transmission is also used in gear transmission systems such as reducers, dividing heads, high-end machine tools, radars, ships, fishing reels, and bicycle sprockets, and has achieved good results.
Gear meshing theory is the basis for face gear tooth surface forming; tooth contact analysis is performed to examine the meshing and bearing contact of the face gear pairs composed of a cylindrical spur gear and the bevel gear. Chang et al. (2000) derived the analytical geometry of the face gear drive and its mathematical model for tooth contact analysis of the face gear, as well as the spur pinion meshing. Litvin et al. (2002a, b) proposed an approach for design, tooth contact analysis, and stress analysis of formate-generated spiral bevel gears. And they also considered a face gear drive with a spur involute pinion; the generation of the face gear is based on the application of a grinding or cutting worm, whereas the conventional method of generation is based on the application of an involute shaper. Liu and Tsay (2002) investigated the contact characteristics of bevel gear pairs with intersected, crossed, and parallel axes. Guingand et al. (2005a, b) presented a procedure for analyzing the instantaneous loaded contact of a face gear and its experimental validation. And they further presented a method of simulating loaded face gear meshing. Tang and Liu (2013) introduced the analytical method based on Hertz theory on normal contact of elastic solids and the numerical method based on the finite-element method, calculating the contact stress of a face gear drive with spur involute pinion. To analyze the transmission performance of a face gear in real working conditions, Wang et al. (2012) investigated a calculation approach for load equivalent error of alignment to analyze the support system and tooth deformation of face gear drives. Lee (2016) proposed a cosine face gear, which is composed of a cosine pinion and a cosine face gear. According to the theory of conjugate tooth surfaces, they created the condition of undercutting for the cosine face gear.
He et al. (2017) obtained the mathematical model of the helical curve face gear and the tooth contact analysis. Li et al. (2017) proposed a face gear tooth modeling that is not based on conjugation theories, and they derived the extreme geometry boundary conditions of face gear teeth according to face gear tooth geometry characteristics. Based on the method of the principal curvatures of the space curve face, Lin et al. (2017) presented the loaded tooth contact analysis of the curve face gear pair. Wu et al. (2018) derived a method, based on the geometry characteristic of the tooth surface, to calculate the points as an even distribution on the tooth surface. Fu et al. (2018) proposed the application of a profile-shifted grinding disk to generate an offset, non-orthogonal and profile-shifted face gear. To solve the problem of the meshing efficiency of spur face gear sliding friction, Dong et al. (2018) proposed a gear based on elastohydrodynamic lubrication theory. Zhou et al. (2019) established an envelope method, according to the geometry characteristic of the shaper tooth surface, and the mathematical model of the face gear tooth surface can be represented as an explicit rather than an implicit one. Zschippang et al. (2000) elaborated on a method for the generation of a face gear with helix angle, shaft angle, and axle offset. Feng et al. (2019) investigated entire tooth surface precise modeling and systematic analysis method for face gear drives with an involute helical pinion. Liu and Zhang (2019) presented a spherical face gear pair by substituting the convex spherical gear for the pinion of a conventional face gear pair.
At present, the research on the meshing method of face gear transmission mainly focuses on coordinate transformation and formula derivation between the tool and target profile. Although some improvements have been made by optimizing the derivation process and transforming the boundary conditions, the induced curvature and other parameters cannot be accurately expressed in a specific equation. Given this, this paper presents data showing that the face gear tooth surface is expressed in the form of the second-order differential equation, and the meshing characteristics of the face gear complex surface can be analyzed by approximating the complex surface of the face gear. In the process of gear design, the visibility of the tooth surface contact state is poor, and finite-element calculation is complicated. There is a lack of unified calculation standards, and the results are difficult to control, making it difficult to guide machining. The long feedback period of face gear design, processing, and testing is seriously affected by the engineering application of a face gear.
Based on the abovementioned research, this paper proposes the digital tooth surface meshing theory of face gears, analyzes the discrete and sampling methods of the face gear surface, studies the analysis method of curvature of the spatial surface, and establishes the contact analysis method of space spheroid. The method can quickly define the tooth surface meshing performance of the face gear, which greatly shortens the face gear sub-design cycle. The design quality and stability are improved, and a foundation is laid for further engineering applications of face gears.
2.1 Discrete sampling
To analyze the meshing process of space-meshing digital teeth, this paper establishes a one-to-one correspondence between the measuring point and the space tooth surface equation. When selecting sampling points on the tooth surface or measuring the tooth surface with the coordinate measuring machine, the sampling points should be evenly distributed as far as possible. In general, 9 points are selected evenly in the direction of the teeth (U direction), and 5 points are selected evenly in the direction of the tooth width (V direction); 45 points are selected in total, and the grid intersection is shown in Fig. 1. This practice shows that if the selection is too few, it is not enough to reflect the shape of the tooth surface. However, if there are too many points, the sampling error of the sampling point may cause a local fluctuation of the tooth surface.
The meshing of the face gear tooth surface is shown in Fig. 2. For any grid node on the tooth surface, the distance rgrid from this point to the origin O2 of the face gear coordinate system and the distance zgrid along the tooth height direction of the face gear can be expressed as
where r2x, r2y, and r2z are the components of the theoretical equation r2(φs,θks) of the face gear along the three directions of the coordinate system.
Equation (1) is a system of binary nonlinear equations about θks and ϕs. For a face gear with given parameters, rgrid and zgrid are presented as numbers. Using the Newton iteration method to solve the above nonlinear equations, the coordinates and normal vectors at each grid point of the face gear tooth surface can be calculated.
2.2 Establish the tooth surface fitting equation
The cubic B-spline function is used to fit the tooth surface sampling points, and the tooth surface fitting equation is obtained as follows:
where
[O2Pi] is a matrix of four rows and four columns of control points.
The control point is obtained by the type value point, and according to the geometrical invariance of the B-spline function, the coordinate transformation of the surface Si is only performed by the coordinate transformation of its control point. Thus, the following formula can be obtained:
The surface normal vector Ni can be obtained as
where
and are the tangent vectors in the U direction and V direction of the surface Si at the point μ1:
2.3 Mathematical model of the tooth surface contact point
In Fig. 3, the solid line represents the situation of the instantaneous meshing contact between pinion 1 and face gear 2 at some point T in the space. As shown in Fig. 3, T1 and T2 are the points on the pinion and the face gear. R1 and R2 are the position vectors of the points T1 and T2 in each coordinate system, respectively. N1 and N2 are the unit normal vectors of the pinion and the face gear at these two points.
In establishing the solution model of the contact point, it can be assumed that pinion 1 is fixed in the coordinate system Σ1. Suppose that when face gear 2 rotated φ2 around its axis P, T1 and T2 would have instantaneous contact at point T, and we have
where (φ2P2)⊗R2 represents when vector R2 rotates φ2 around the axis P2. The equations consist of five equations with five unknowns (u1, v1, u2, v2, φ2). For the convenience of further solution, Eq. (5) is converted. The following equation can be obtained:
where in xj stands for the five unknowns (u1, v1, u2, v2, φ2); [aj,bj] is the corresponding interval for xj; and |R| is the length of the vector R. Equation (6) transforms the problem of solving nonlinear equations in a certain interval into the minimum value optimization problem with constraints. In Eq. (6), Q(Q≥1) is introduced to reduce the influence of the position vector at the beginning of the search and to speed up the search. This is because in the initial search the change in the length of the position vector difference is not the same magnitude as the change in the length of the unit normal vector, and its value can be selected according to the specific situation.
When using this method to solve the contact point of the tooth surface, the pinion can be rotated around its axis P1 to a certain meshing position and fixed; the surface parameters of the contact point and the rotation angle φ20 of the large wheel at this moment can be solved. Then, the pinion in turn rotates Δφ1 around its axis P1, and it solves the rotation φ2 of the face gear and calculates the angle increment of the face gear.
Suppose that the pinion is rotated around the axis P1 by angle Δφ1, then the tooth surface equation is . The one corresponding to the angle of increment of a face gear is Δφ2, and the face gear tooth surface equation is . The tooth surfaces and contact at point T′, and the first-class basic quantity of the tooth surface and are given as
The second-class basic quantity is expressed as follows:
where n is the normal vector at point ; is the first derivative of the tooth surface i on the parameter ui; and is the second derivative of the tooth surface i on the parameter ui.
The binary vector function r(u,v) has two parameters u and v. When u and v change, its endpoint M will draw a continuous surface S in space, and its equation can be expressed as
Suppose that M0 is any point on the surface S, and its surface coordinates are u0 and v0. If we let v=v0 and only change u, we can get a curve passing through M0 on the surface S. Similarly, if we let u=u0 and only change v in Eq. (1), we can get a curve passing through M0 on the surface S. According to the properties of the space surface, we can solve the first-order and second-order partial derivatives.
The first fundamental homogeneous equation of the surface is expressed as follows:
where E, F, and G are the coefficients of the first fundamental homogeneous equation, respectively.
The second fundamental homogeneous equation of the surface is expressed as follows:
where L, M, and N are the coefficients of the second fundamental homogeneous equation, respectively.
The unit normal vector of surface S at M0 is expressed as follows:
Substituting the coefficient of the first fundamental homogeneous equation into Eq. (14), then
The normal curvature kn of the surface is expressed as follows:
where β is the main normal vector, and k is the curvature of the curve r at M0; θ is the angle between β and n.
Substituting the coefficients of the first basic homogeneous form and the second basic homogeneous form, the formula for calculating the normal curvature is expressed as follows:
The torsion of curvature at points M along is expressed as follows:
We introduce the coefficients of the first and second fundamental homogeneous equations to obtain the calculation formula for the short-range torsion rate.
Then, we have
Let g1 and g2 be the main directions. The principal curvature of direction g1 is k1, and the principal curvature in the direction g2 is k2. The angle between α and g1 is θ. According to the Euler formula and the Bertrand formula, we have the following:
Set the angle between α1 and g1 to φ, and the angle between α2 and g1 to 90∘ +φ. From Eq. (21), the normal curvature and short-range torsion of the α1 direction and the α2 direction are expressed as follows:
When we substitute them to kn1kn2−(τg1)2, we have the following:
According to the above basic formula of the surface, the curvature characteristics of the space free surface are analyzed. The simulation results of the face gear are shown in Fig. 4.
4.1 Curvature of the conjugate surface
Knowing two surfaces, when solving the conjugate motion relationship of the surfaces in the contact process, the average curvature and Gaussian curvature are used to describe the characteristics of the points on the surface. We suppose that the two curvatures are denoted by k1 and k2 and are determined by the following equations.
where E, F, and G are the first fundamental quantities of the surface, and L, M, and N are the second fundamental quantities of the surface.
The average curvature H is a key indicator of curvature, and the Euler equation can prove that the average value of normal curvature of a point on the surface along two orthogonal directions is the same; it equals the average curvature. This shows that the curvature of a point only considers average curvature. Therefore, when the regional structure is simplified, the substituted constructed surfaces must have equal Gaussian curvature and mean curvature. In other words, it should have the same principal curvature and main direction. In some simple secondary, rotating surfaces, such as ellipsoids, cylinders, and hyperboloids, the longitude lines and latitude lines are geodesics, and the measuring torque is zero. Therefore, the direction of the longitude line and latitude line becomes the main direction and the main curvature, which can replace the conjugate surface contact area.
4.2 Equations and expressions of the ellipsoid
According to the surface feature of the initial point, the surface can be simplified to the elliptical surface, cylindrical surface, and hyperboloid; all three types can be written as general statements.
In the equation, , and a and b are the lengths of the long axis and the short axis, respectively.
And this assumes b≥a, so
When , it is a hyperbola.
When , it is a circular cylinder with a radius of a.
When , it is the rotation of the ellipse.
Suppose that these three types of surfaces are all rotating surfaces with the Y axis as the rotation axis; the longitude line as a circle; and the latitude line as an elliptical spiral, a straight line, or a hyperbola, respectively. The normal of the ellipsoid is N=[x fy z]T, and its direction points to the outside; the normal curvature of the longitude line and the latitude line of the ellipsoid are given as
4.3 Replacement of the conjugate surface with an ellipsoid
When a point P=[a 0 0]T on the surface of the ellipsoid matches a point on the conjugate surface, its normal direction should be the same as the fixed point. The main direction of P is the same as that of the specified point on the conjugate surface, and the principal curvature is equal. According to the characteristics of the ellipsoid, the two main directions of the P points should be the longitude line and the latitude line, and the normal curvature of the longitude line and latitude line should be
However, the absolute value of two normal curvatures is expressed as and . Because b≥a, so . This shows that the y axis is usually the long axis of the ellipsoid. It is assumed that the two main curvatures on the conjugate surface have the following relation: . When the ellipsoid replaces the hyperboloid, i.e., kg=k1 and kt=k2, we can deduce that and .
After the ellipsoid replaces the conjugate surface, the problem of solving conjugate surfaces becomes the problem of solving the minimum distance between two points. Suppose that the two ellipsoids S1 and S2 are placed in two coordinate systems σ1(O1−x1y1z1) and σ2(O2−x2y2z2), and S1 and S2 can be, respectively, expressed as follows:
The normal vector of the ellipsoid can be expressed as
5.1 Minimum distance between ellipsoid and ellipsoid
Assume that the rotation matrix from σ2 to σ1 is expressed as follows:
The vector between two coordinate centers (two ellipsoid centers) can be expressed as
Based on the conjugate theory, the two points with the minimum distance are usually on two conjugate surfaces, the normal lines of the two points are parallel to each other, and the vectors between the two points are parallel to the normal line. Therefore, we have
where Kn and Kr are two unknown coefficients that can be expressed as
The minimum distance between two points can be obtained from the eight equations (Eqs. 32 and 34). To obtain the analytical solution, the hypothesis of the ellipsoid should be further simplified.
5.2 Analytical solution from point to ellipsoid
The ellipsoid S2 is simplified to a point, where x2, y2, and z2 are zero. According to the above derivation, we can obtain
This can be obtained by substituting Eq. (35) into Eq. (32).
where
Four analytical solutions can be obtained from Eq. (36), two of which are real solutions and the other two are imaginary solutions. Figure 5 shows the diagram of the real solution. The imaginary solution shown in Fig. 6 should be given up. The two real solutions are the nearest A1 and the farthest A2 from P. Get rid of the farthest point according to the requirements. Then, point A1 of the analytical solution is obtained, which is the closest point of the ellipse to P.
After obtaining the A1 point on the ellipsoid, the shortest distance point B1 from A1 to S2 can be solved by repeating the solution of the four polynomials of A1 to the ellipsoid S2. Thus, an iterative process is completed. Figure 6 shows the points Ai and Bi that have been iterated over six times. The minimum distance can be obtained through finite iteration and the iteration termination condition.
where ε1 and ε2 represent the convergence precision.
5.3 The analytical solution of the ball to the ellipsoid
The main reason for the low solution speed is that the ellipsoid surface features are not used. When the ellipsoid is simplified to a point, all the curvature characteristics of the point disappear. Therefore, the point can be reduced to a sphere according to the curvature characteristic.
In general, the distance between the center of the sphere and the center of the ellipsoid is the distance from the sphere to the ellipsoid. Therefore, the shortest distance between the two ellipsoids can be reduced to find the center of the sphere.
We can derive kt≥kg; hence, the curvature of the sphere is kt. The position vector roof of the sphere center can be derived from the following equation.
This indicates that the center of the sphere is usually on the y axis, and it is independent of the other two variables x and z. The iterative process is shown in Fig. 7.
The conjugate of the surface shows that the two surfaces revolve around their axis; the rotation angles are φ1 and φ2. When φ1 is a constant, there must be φ2 to make the two surfaces in contact in a conjugate form. The rotation surface S2 should rotate at an angle to make the conjugate surface contact. The two rotating surfaces are very close when in contact, and their radius of rotation is very large, so the rotational motion of S2 can be simplified as a translation. Assume that the unit vector of the translation direction is
where δpx, δpy, and δpz are only related to φ2. Generally, the direction of translation is not along the shortest path between the two ellipsoids, but with an angle. Therefore, the distance along the translation path to the ellipsoid S2 can be simplified as the projection of the shortest distance in the translation direction. Therefore, the approximate distance l can be expressed as
When l is positive, it moves forward. On the contrary, when l is negative, it moves in the opposite direction. Figure 8 shows the process of the ellipsoid S2 approaching S1, which is an iterative process. When the direction δp of the shift is the same as the direction of the shortest distance, the root of the equation can be solved step by step. Conversely, when the angle between the two surfaces becomes larger, the impact of the ellipsoid curvature on the approximation process will be lower.
Apply the above analysis method to analyze the tooth contact of the gear pair. First, the main curvature and main direction of the tooth surface are calculated. Then, the regional structure of the initial calculation point is simplified to the ellipsoid based on the simplifying principle. ECA is applied to a series of conjugate contact points on the tooth surface, and the meshing line is available. Finally, the relative main direction and the main curvature can be calculated according to the curvature characteristics of the two surfaces. The size and direction of the meshing point can also be calculated.
Taking the parameters shown in Table 1 as an example, the calculated contact cloud diagram of the face gear tooth surface is shown in Fig. 9. The tooth surface contact path of the front gear can be seen from the figure. To avoid excessive tooth-bottom undercut and tooth-top sharpening, the face gear width is designed to be 32 mm under the conditions of processing. The surface contact trace of the face gear is directed from the outer tooth top to the inner tooth bottom, which can meet the requirements of face gear transmission meshing contact. From the above analysis, it can be seen that the application of ellipsoidal surface contact analysis theory can quickly determine the meshing characteristics of the face gear tooth surface and effectively shorten the development cycle of the face gear.
This paper presents an ellipsoidal contact analysis method for the meshing tooth surface of a face gear. Ellipsoidal substituting of the meshing surface can simplify the choke contact process and avoid the singularity entering the analysis area, thus improving the iteration speed and stability. The numerical engagement method of the ellipsoid arc of high-order face gears can be extended to the contact process analysis of other complex surfaces. It provides a theoretical basis for the rapid integrated optimization design of face gears. Some conclusions are given as follows.
- 1.
According to the characteristics of the face gear, the preferred method of the face gear flank sample point is established, the flank sampling point is meshed by three B-spline functions, the face gear flank fitting equation is derived, and a mathematical model is formulated to solve the contact point of the fitted flank using the composite method.
- 2.
With the two-curve direction as the reference direction, the curvature of the surface at the determining point and the short-range deflection rate are obtained.
- 3.
To simplify the solution of the conjugate motion relationship in the theory of flank conjugate, it is proposed to replace the conjugate surface with an elliptic body to simplify the digital iterative process into an analytical solution.
All the code and data used in this paper can be obtained upon request to the corresponding author.
XC and HZ conceived the presented idea. XC and YL established an overall research framework and the model. YL conducted data calculation for the overall paper. All the authors discussed the results and contributed to the final paper.
The contact author has declared that none of the authors has any competing interests.
Publisher’s note: Copernicus Publications remains neutral with regard to jurisdictional claims in published maps and institutional affiliations.
The authors would like to thank anonymous reviewers for their valuable comments and suggestions that enabled us to revise the paper.
This research was funded by the Science Research Funding Project of Education Department of Liaoning Province (grant no. LJKZ0603) and the Doctoral Research Start-up Fund Project of Liaoning Province (grant no. 2022-BS-308).
This paper was edited by Daniel Condurache and reviewed by two anonymous referees.
Chang, S. H., Chung, T. D., and Lu, S. S.: Tooth contact analysis of face gear drives, Int. J. Mech. Sci., 42, 487–502, https://doi.org/10.1016/S0020-7403(99)00013-2, 2000.
Dong, H., Liu, Z.-Y., Duan, L.-L., Hu, Y.-H.: Research on the sliding friction associated spur-face gear meshing efficiency based on the loaded tooth contact analysis, PLoS ONE, 13, e0198677, https://doi.org/10.1371/journal.pone.0198677, 2018.
Feng, G., Xie, Z., and Zhou, M.: Geometric design and analysis of face-gear drive with involute helical pinion, Mech. Mach. Theory, 134, 169–196, https://doi.org/10.1016/j.mechmachtheory.2018.12.020, 2019.
Fu, X., Fang, Z., Cui, Y., Hou, X., and Li, J.: Modelling, design and analysis of offset, non-orthogonal and profile-shifted face gear drives, Adv. Mech. Eng., 10, 1–12, https://doi.org/10.1177/1687814018798250, 2018.
Guingand, M., Vaujany, J. P., and Jacquin, C. Y.: Quasi-static analysis of a face gear under torque, Comput. Method. Appl. M., 194, 4301–4318, https://doi.org/10.1016/j.cma.2004.10.010, 2005a.
Guingand, M., Vaujany, J. P., and Icard, Y.: Analysis and optization of the loaded meshing of face gear, J. Mech. Design, 127, 135–143, https://doi.org/10.1115/1.1828459, 2005b.
He, C. and Lin, C.: Analysis of loaded characteristics of helical curve face gear, Mech. Mach. Theory, 115, 267–282, https://doi.org/10.1016/j.mechmachtheory.2017.05.014, 2017.
Lee, C. K.: The Mathematical Model and the Condition of Under cutting for the Cosine Face Gear Drive Generated by a Cosine Rack, in: 2016 International Conference on Materials, Manufacturing and Mechanical Engineering, Beijing, 30–31 December 2016, 166–170, https://doi.org/10.12783/dtmse/mmme2016/10101, 2016.
Li, Z., Fan, J., and Zhu, R.: Construction of Tooth Modeling Solutions of Face Gear Drives with an Involute Pinion, IJST-T. Mech. Eng., 42, 35–39, https://doi.org/10.1007/s40997-017-0074-4, 2017.
Lin, C., He, C., Gu, S., and Wu, X.: Loaded tooth contact analysis of curve face gear pair, Adv. Mech. Eng., 9, 1–10, https://doi.org/10.1177/1687814017727473, 2017.
Litvin, F. L., Fuentes, A., Fan, Q., and Handschuh, R. F.: Computerized de sign, simulation of meshing, and contact and stress analysis of face milled formate generated spiral bevel gears, Mech. Mach. Theory, 37, 441–459, https://doi.org/10.1016/S0094-114X(01)00086-6, 2002a.
Litvin, F. L., Fuentes, A., Zanzi, C., Pontiggia, M., and Handschuh, R. F.: Facegear drive with spur involute pinion: geometry, generation by a worm stress analysis, Comput. Method. Appl. M., 191, 2785–2813, https://doi.org/10.1016/S0045-7825(02)00215-3, 2002b.
Liu, C. C. and Tsay, C. B.: Contact characteristics of beveloid gears, Mech. Mach. Theory, 37, 333–350, https://doi.org/10.1016/S0094-114X(01)00082-9, 2002.
Liu, L. and Zhang, J.: Meshing characteristics of a sphere–face gear pair with variable shaft angle, Adv. Mech. Eng., 11, 1–10, https://doi.org/10.1177/1687814019859510, 2019.
Tang, J. and Liu, Y.: Loaded multi-tooth contact analysis and calculation for contact stress of face-gear drive with spur involute pinion, J. Cent. South Univ., 20, 354–362, https://doi.org/10.1007/s11771-013-1495-x, 2013.
Wang, Y., Wu, C., Gong, K., Wang, S., Zhao, X., and Lv, Q.: Loaded tooth contact analysis of orthogonal face-gear drives, P. I. Mech. Eng. C-J. Mec., 226, 2309–2319, https://doi.org/10.1177/0954406211432976, 2012.
Wu, Y., Zhou, Y., Zhou, Z., Tang, J., and Ouyang, H.: An advanced CAD/CAE integration method for the generative design of face gears, Adv. Eng. Softw., 126, 90–99, https://doi.org/10.1016/j.advengsoft.2018.09.009, 2018.
Zhou, Y., Wu, Y., Wang, L., Tang, J., and Ouyang, H.: A new closed-form calculation of envelope surface for modeling face gears, Mech. Mach. Theory, 137, 211–226, https://doi.org/10.1016/j.mechmachtheory.2019.03.024, 2019.
Zschippang, H. A., Weikert, S., Kucuk, K. A., and Wegener, K.: Face-gear drive: Geometry generation and tooth contact analysis, Mech. Mach. Theory, 142, 487–502, https://doi.org/10.1016/j.mechmachtheory.2019.103576, 2000.
- Abstract
- Introduction
- Tooth surface discretization and fitting
- Curvature analysis of space monolithic free-form surface
- Generative analysis of the discrete curvature asymptotic surface
- Ellipsoid contact analysis (ECA)
- Conclusions
- Code and data availability
- Author contributions
- Competing interests
- Disclaimer
- Acknowledgements
- Financial support
- Review statement
- References
- Abstract
- Introduction
- Tooth surface discretization and fitting
- Curvature analysis of space monolithic free-form surface
- Generative analysis of the discrete curvature asymptotic surface
- Ellipsoid contact analysis (ECA)
- Conclusions
- Code and data availability
- Author contributions
- Competing interests
- Disclaimer
- Acknowledgements
- Financial support
- Review statement
- References