the Creative Commons Attribution 4.0 License.
the Creative Commons Attribution 4.0 License.
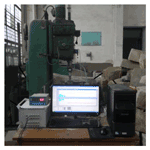
Drilling performance analysis of impregnated micro bit
Zhangping Ren
Yingxin Yang
Yousheng Chen
Gao Nie
Leichuan Tan
Hao Peng
Zijie Li
Xiaojing Chen
Meng Li
Haitao Ren
Long Zuo
The cutting mechanical properties of impregnated diamond bit depend on the performance of its cutting elements. Aiming at the factors affecting the cutting element performance of impregnated diamond bit, the laboratory rock breaking experiment of impregnated micro bit is carried out. The results show that the breaking work ratio and unit wear first decrease and then increase with the increase of diamond particle size and concentration when drilling sandstone; the rock breaking efficiency and wear resistance are the highest when the concentration is 125 %. The breaking work ratio first decreases and then increases with the increase of diamond particle size when drilling limestone; the rock cutting efficiency is the highest when the concentration is 100 %. With the increase of diamond particle size, the breaking work ratio increases and the unit wear decreases when drilling granite; the rock cutting efficiency and wear resistance are the highest when the concentration is 150 %.
- Article
(1745 KB) - Full-text XML
- BibTeX
- EndNote
The tight and low-permeability sandstone gas reservoir in western Sichuan belongs to a complex gas field with low permeability, compactness, and low porosity (Ren, 2011), and the general bit is difficult to meet the needs of actual drilling. Relatively speaking, impregnated diamond bit has obtained obvious footage and mechanical penetration rate in the drilling process of extremely hard and highly abrasive formation by virtue of its special rock breaking mechanism (Wang, 2009; Glowka, 1986; Yang and Song, 2019; Yang, 2010; Randy and Baker, 2010). The performance of cutting elements determines the rock cutting efficiency. Therefore, improving the cutting performance of cutting elements is of significance to the drilling efficiency and the service life of the bit. In addition, the performance of matrix also has an important impact on bit drilling efficiency (Tim et al., 2000; Ersky, 1976; Tsunehisa and Takash, 2014). The concentration of diamond varies with the type of rock. Selecting the diamond concentration suitable for the formation is conducive to improving the bit penetration rate (Zuo, 2015; Pan et al., 2002). Using impregnated inserts as cutting elements has created a world well section record of 1755 m, with an average rate of penetration (ROP) of 5.52 m h−1 (Hou, 2010). The coupling bionic theory is applied to the structural design of impregnated diamond cutting elements, which have higher drilling efficiency and longer service life (Sun et al., 2013). The thermally stable impregnated teeth made of new granulation process and impregnated materials are used on the bit. During drilling in highly abrasive formations, the wear resistance is greatly improved (Ronen, 2001; Gavito, 1994). The influence of different drilling conditions on the cutting efficiency of impregnated elements is studied by taking different component ratios of concrete cement as the analysis object and sintering process, and the optimal weight on bit (WOB) range is obtained (Abtahi et al., 2011; Dong et al.,2013).
In order to improve the efficient drilling of impregnated diamond in complex difficult and strong abrasive formations, this paper carries out the laboratory test of impregnated micro bit and obtains the influence law of relevant parameters (including diamond concentration, particle size, WOB, and rotary speed) on impregnated teeth, so as to provide basis for the design of impregnated bit.
The performance of cutting elements of impregnated diamond bit mainly includes cutting efficiency and wear resistance (service life). The cutting performance depends on the performance of impregnated diamond cutting elements. Therefore, this paper studies the cutting performance of pregnant insert by carrying out micro drilling tests with different formulas. Mastering the influence law of different diamond parameters and drilling parameters on the cutting efficiency and wear resistance of impregnated bit under the “micro cutting” rock breaking, so as to provide a theoretical basis for the design of impregnated bit.
The micro drilling experiment is carried out on the material abrasiveness machine (as shown in Fig. 1). The experimental device includes power device, loading device, measuring device, hydraulic circulation device, micro bit, and rock sample. The micro bit is fixed on the pressure sensor connected with the material abrasiveness machine, and an O-ring groove is set above and below the position where the strain gauge is pasted to prevent the coolant from splashing out during the test, thus affecting the stability of the signal. The signals of displacement sensor and pressure sensor are converted to a computer through strain gauge for data acquisition. At the same time, the FA2204B One-ten-thousandth Electronic Balance Scale is used to measure the wear of micro bit, as shown in Fig. 2. Three kinds of rocks representing different formation hardness are used in the test, namely sandstone (medium hard), limestone (hard), and granite (high hard). The rock sample size is 300 cm × 100 cm × 100 cm, and the rock mechanical properties are shown in Table 1.
3.1 Formula selection and manufacture of impregnated teeth
Four diamond particle sizes of 18–20, 25–30, 30–35, and 60–70 mesh, and four diamond concentrations of 75 %, 100 %, 125 %, and 150 % (400 % concentration system) were selected in the experiment. Each particle size is matched with four concentrations, a total of 16 kinds of impregnated teeth are required. The matrix of impregnated element adopts the 63# formula with low sintering temperature and good matrix hardness, wear resistance, and impact toughness. The material ratio is 35wc + 5Ni + 5MN + 2CO + 52bronze. The basic properties are shown in Table 2. The diameter of the impregnated teeth is 14 mm and the height is 30 mm. The sintered part of the impregnated teeth is shown in Fig. 3, for which the concentrations are 75 %, 100 %, 125 %, and 150 %, respectively, from top to bottom in Fig. 3a–d; the particle sizes from top to bottom are 18–20, 25–30, 30–35, and 60–70 mesh, respectively.
3.2 Experimental process
During the experiment, it is necessary to test the cutting efficiency and wear of 16 kinds of impregnated teeth with different diamond particle size and concentration under four kinds of WOB (50, 80, 125, and 200 kg) and four kinds of rotary speeds (90, 125, 180, and 250 r min−1). In order to ensure that the micro bit can meet the rock stability, reduce the vibration, and achieve the effect of cooling the bit and removing rock cuttings during micro drilling (the processed micro bit is shown in Fig. 4). During the drilling process, the record is started after drilling 1 mm, and stopped after reaching 5 mm. Each group is repeated for 5–8 times. In order to accurately test the wear amount of pregnant inlaid teeth, the remaining mass of pregnant inlaid teeth shall be weighed every 30 mm. The drilling process is shown in Fig. 5.
4.1 The drilling bottom hole
The bottom hole after crushing rock samples with micro bit is shown in Figs. 6–8. At the same depth of drilling, granite is the longest, the limestone is the next, and the sandstone is the shortest. The time of diamond parameters under different particle size and concentration in drilling granite is obviously different, and the action time of impregnated teeth with large particle size and high concentration is shorter when WOB and rotary speed are constant. There is a thin layer of compacted rock powder at the bottom of the cutting groove for large-size diamond, which is difficult to wash away. However, the small-size diamond has small cutting grooves at the bottom hole, and the edges are neat, indicating that the contact area between diamond particles and rock is very small, the specific pressure is large, and the large-size diamond has obvious cutting grooves at the bottom hole.
4.2 Rock cutting efficiency
The specific work of unit volume crushing is the external load work required for drilling and crushing unit volume rock, which is an important index to evaluate the cutting efficiency of impregnated bit. The smaller the breaking work ratio, the higher the cutting efficiency (Cai et al., 2015; Rojek et al., 2011).
The breaking work ratio of granite, limestone, and sandstone under different particle sizes and concentrations is shown in Fig. 9. It can be seen from Fig. 9(a) that the breaking work ratio first decreases and then increases with the increase of diamond particle size when drilling sandstone. When the particle size is 25–30 mesh, the breaking work ratio is the smallest, and the minimum values are 1.67, 1.62, 1.52, and 1.83 J mm−3, respectively, at 75 %, 100 %, 125 %, and 150 % concentrations. That is, the impregnated micro bit has the highest rock cutting efficiency, which is about 23 %–26 % higher than other particle sizes, when the particle size is 25–30 mesh. When the particle size is constant, the breaking work ratio first decreases and then increases with the increase of concentration, the crushing specific work is the smallest, and its minimum values under different particle sizes are 1.75, 1.52, 1.71, and 2.06 J mm−3, respectively, when the concentration is 125 %. That is, the rock cutting efficiency of impregnated micro bit drilling into sandstone is the highest when the concentration is 125 %.
From Fig. 9b, the breaking work ratio first decreases and then increases with the increase of diamond particle size when drilling limestone. The breaking work ratio is the smallest when the particle size is 30–35 mesh, and the minimum values are 2.88, 1.87, 4.11, and 3.56 J mm−3, respectively, under different concentrations. That is, the rock cutting efficiency of impregnated micro bit is the highest when the particle size is 30–35 mesh. Compared with other particle sizes, the rock cutting efficiency is increased by about 42 %–61 %. When the particle size is constant and the concentration is 100 %, the breaking work ratio is the smallest, and its minimum values are 2.82, 2.43, 1.87, and 4.85 J mm−3, respectively, under different particle sizes. That is, when the concentration is 100 %, the rock cutting efficiency of impregnated micro bit drilling limestone is the highest.
It can be seen from Fig. 9c that the breaking work ratio increases with the increase of diamond particle size when drilling granite. The breaking work ratio is relatively close when the particle size is 18–20, 25–30, and 30–35 mesh, that is, the rock cutting efficiency of impregnated micro bit is the same under these three particle sizes. The breaking work ratio is the highest when the particle size is 60–70 mesh. The rock cutting efficiency is the lowest. The breaking work ratio is the smallest when the concentration is 150 %, and its minimum values are 1.85, 1.89, 1.98, and 4.61 J mm−3, respectively, under different particle sizes. That is, the rock cutting efficiency of impregnated micro bit drilling granite is the highest when the concentration is 150 %.
Figure 10 shows the breaking work ratio of three rock samples at different rotary speed. The breaking work ratio of granite, limestone, and sandstone first decreases and then increases with the increase of rotary speed, and the value is the smallest at 180 r min−1, with the minimum values of 2.57, 1.95, and 1.03 J mm−3, respectively. That is, the rock cutting efficiency of three rock samples drilled with impregnated micro bit is the highest when the rotary speed is 180 r min−1, the breaking work ratio is increased by 34.3 %, 48.1 %, and 38.3 %, respectively, compared with other speeds.
The breaking work ratio of the three rock samples under different WOB is shown in Fig. 11. The breaking work ratio of granite increases with the increase of WOB. The breaking work ratio is the smallest when the WOB is 100 kg, and its value is 3.778 J mm−3, that is, the rock cutting efficiency of impregnated micro bit is the highest at this WOB. The breaking work ratio of limestone and sandstone is the smallest, and the minimum values are 2.25 and 0.93 J mm−3, respectively, when the WOB is 160 and 250 kg, respectively. Among the three rock samples, breaking work ratio is the smallest when drilling sandstone, limestone is the second, and granite is the largest, that is, the rock cutting efficiency of impregnated micro bit when breaking granite is the lowest, limestone is the second, and sandstone is the highest. The main reason is that sandstone is softer than limestone and granite; the rock cutting efficiency of sandstone is higher than that of the other two rock samples under certain drilling conditions.
4.3 Wear resistance
The wear resistance of impregnated teeth is reflected by the change of wear amount. The milligram of weight lost by impregnated teeth per unit depth of drilling indicates the wear speed of the bit, which is used as a quality index to measure the wear resistance of the bit.
The unit wear of granite, limestone, and sandstone under different particle size and concentration is shown in Fig. 12. It can be seen from Fig. 12a that the unit wear first decreases and then increases with the increase of diamond particle size when drilling sandstone. The unit wear is the smallest when the particle size is 25–30 mesh, and the minimum values are 1.16, 1.01, 0.92, and 1.22 mg mm−1, respectively, at 75 %, 100 %, 125 %, and 150 % concentrations. That is, the wear resistance of impregnated micro bit is the highest when the particle size is 25–30 mesh, which improved by about 22.1 %, 22.9 %, 21.4 %, and 10.9 %, respectively, compared with other particle sizes. The unit wear first decreases and then increases with the increase of concentration when the particle size is constant. When the concentration is 125 %, the unit wear is the smallest, and the minimum values are 1.08, 0.92, 1.06, and 1.17 mg mm−1, respectively, under different particle sizes, that is, the wear resistance of impregnated micro drill head drilling sandstone is the highest when the concentration is 125 %.
From Fig. 12b, the unit wear is the smallest when the particle size is 30–35 mesh, and the minimum values are 2.74, 2.3, 2.49, and 2.55 mg mm−1, respectively, under different concentrations, that is, the wear resistance of impregnated micro bit is the highest when the particle size is 30–35 mesh, and its wear resistance is improved by about 17 %–22 % compared with other particle sizes. When the particle size is certain, the unit wear is the smallest when the concentration is 100 %, and the minimum values are 2.53, 2.59, 2.3, and 2.79 mg mm−1, respectively, under different particle sizes, that is, the wear resistance of impregnated micro bit drilling limestone is the highest when the concentration is 100 %.
As can be seen from Fig. 12c, the unit wear decreases with the increase of diamond particle size when drilling granite. The unit wear is equivalent when the particle size is 30–35 and 60–70 mesh, that is, the wear resistance of the two particle sizes is equivalent. When the particle size is certain, the unit wear amount is the smallest at the concentration is 150 %, and the minimum values are 3.98, 2.49, 0.41, and 0.21 mg mm−1, respectively, under different particle sizes, that is, the wear resistance of impregnated micro bit drilling granite is the highest when the concentration is 150 %.
Figure 13 shows the unit wear of three rock samples at different speeds. The unit wear of granite first increases and then decreases with the increase of rotary speed. The unit wear of granite is the smallest when the rotary speed is 90 r min−1, with a value of 1.252 mg mm−1, that is, the wear resistance of impregnated micro bit is the highest when the rotary speed is 90 r min−1, and the unit wear of limestone and sandstone is the smallest, the values are 1.16 and 1.103 mg mm−1, respectively, when the rotary speed is 90 and 125 r min−1.
The unit wear of the three rock samples under different WOB is shown in Fig. 14. It can be seen that the unit wear of sandstone decreases with the increase of WOB, and the minimum value is 1.65 mg mm−1 at 400 kg, that is, the wear resistance of impregnated micro bit is the highest when the WOB is 400 kg. The unit wear of limestone and granite is the smallest when the WOB is 160 and 250 kg, respectively, and the values are 2.52 and 2.26 mg mm−1, respectively, that is, the wear resistance of impregnated micro bit is the highest when the WOB is 160 and 250 kg. Among the three rock samples, the unit wear is the smallest when drilling sandstone, followed by limestone and granite, that is, the wear resistance of impregnated micro bit when breaking granite is the lowest, limestone is the second, and sandstone is the highest.
-
When the particle size is 25–30 mesh, the breaking work ratio is the smallest, and the minimum values are 1.67, 1.62, 1.52, and 1.83 J mm−3, respectively, the rock cutting efficiency and wear resistance are the largest compared with other particle sizes, which are increased by about 26 % and 22.9 %, respectively. The rock cutting efficiency and wear resistance of impregnated micro bit drilling sandstone are the highest when the concentration is 125 %.
-
When the particle size is 30–35 mesh, the minimum breaking work ratios are 2.88, 1.87, 4.11, and 3.56 J mm−3, respectively, the rock cutting efficiency and wear resistance are the largest, which are about 61 % and 22 %, respectively. The rock cutting efficiency of impregnated micro bit drilling limestone is the highest when the concentration is 100 %. The rock cutting efficiency and wear resistance of impregnated micro bit drilling granite are the highest when the concentration is 150 %, and the minimum breaking work ratios are 1.85, 1.89, 1.98, and 4.61 J mm−3, respectively.
-
The minimum breaking work ratio of granite, limestone, and sandstone is 2.57, 1.95, and 1.03 J mm−3, respectively, when the rotary speed is 180 r min−1, and the rock cutting efficiency of granite is the highest when the WOB is 100 kg. Limestone and sandstone have the minimum breaking work ratio and are 2.25 and 0.93 J mm−3, respectively, when the WOB is 160 and 250 kg, respectively.
-
The wear resistance of limestone and sandstone is the highest when the rotary speed is 90 and 125 r min−1, respectively. When drilling sandstone, the wear resistance of impregnated micro bit is the highest when the WOB is 400 kg. And limestone and granite have the highest wear resistance when the WOB is 160 and 250 kg, respectively.
-
Through the “micro cutting” mode, the influence rules of diamond particle size, concentration, WOB, rotary speed on cutting efficiency and wear resistance are obtained and master the adaptability of impregnated micro bit to different rocks. It has an important guiding significance for the design and application of impregnated diamond.
All the data used in this paper can be obtained via request from the corresponding author.
DS is mainly responsible for the analysis and processing of the paper structure, grammar, and experiment. YY and HR are mainly responsible for the processing of the paper structure and experiment. ZR and LZ mainly revised the grammar of the paper and carried out experimental tests. YC, GN, LT, HP, ZL, XC, and ML mainly helped to solve the sentences in the paper.
The contact author has declared that none of the authors has any competing interests.
Publisher's note: Copernicus Publications remains neutral with regard to jurisdictional claims in published maps and institutional affiliations.
We appreciate the comments and suggestions from the reviewers and editor very much, which are valuable in improving the quality of our paper.
This paper was edited by Bahman Azarhoushang and reviewed by two anonymous referees.
Abtahi, A., Butt S., and Molgarrd, J.: Wear Analysis and Optimization on Impregnated Diamond Bits in Vibration Assisted Rotary Drilling, 45th U. S. Rock Mechanics/Geomechanics Symposium, American Rock Mechanics Association, Sen Francisco, CA ,26–29 June, 2011.
Cai, C., Wu, K. S., and Yuan, X. H.: Research and application of crushing specific work evaluation model based on rock damage constitutive model, Geotechnical Mechanics 36, 2576–2584, 2015 (in Chinese with English abstract).
Dong, H. F., Lu, Y., and Li, W. S.: Structure and tribological properties of Fe-based impregnated diamond abrasive-head prepared by different sintering technology, Fenmo Yejin Cailiao Kexue yu Gongcheng/Materials Science and Engineering of Powder Metallurgy, 18, 125–131, 2013.
Ersky, G. W.: The Influence of Machine and tool parameters on the drilling of concrete with industrial diamond bit, IDR, 382–84, 1976.
Gavito, D. G.: Bit Profile and Cutter Arrangement Have Significant Effect on PDC Bit Performance Drill & Completion, 9, 167–175, https://doi.org/10.2118/20415-PA, 1994.
Glowka, D. A.: The use of single-cutter data in the analysis of PDC bit designs, Int. J. Rock. Mech. Min., 27, A98–A99, https://doi.org/10.1016/0148-9062(90)95132-K, 1986.
Hou, F.: Application of impregnated diamond bit at home and abroad, Inner Mongolia Petrochemical Industry, 5, 21–23, 2010.
Pan, B., Shi, D., and Yang, K.: Effect of diamond particle size on the performance of impregnated diamond bit, Coalfield Geology and Exploration, 30, 62–64, 2002 (in Chinese with English abstract).
Randy, B. M. and Baker, H.: Improving Marcellus shale using PDC bits with optimized torque management technology, cutting structure aggressiveness and unique roller cone steel tooth cutting structure SPE 139102, https://doi.org/10.2118/139102-MS, October 13–15, Morgantown, West Virginia, USA, ISBN 978-1-55563-310-3, 2010.
Ren, S.: Research and application of large scale fracturing technique for low permeability and tight gas reservoir in West Sichuan, East China: China University of Petroleum, https://doi.org/10.7666/d.y2013702, 2011 (in Chinese with English abstract).
Rojek, J., Onate, E., and Labra, C.: Discrete element simulation of rock cutting, Int. J. Rock. Mech. Min., 48, 996–1010, https://doi.org/10.1016/j.ijrmms.2011.06.003, 2011.
Ronen, A.: Friction reducing surface texturing in reciprocating automotive component, Tribol. T., 44, 359–366, 2001.
Sun, Y., Liu, D., and Gao, K.: Development of new coupling bionic impregnated diamond oil bit, Journal of Jilin Science: Engineering Edition, 43, 25–36, https://doi.org/10.7964/jdxbgxb201306022, 2013 (in Chinese with English abstract).
Tim, B., Geo, D., and Keith, J.: New Technology in Diamond Drill Bits Improves Performance in Variable Formations, SPE 59113, the IADC/SPE Drilling Conference, New Orleans, Louisiana, February, https://doi.org/10.2118/59113-MS, 2000.
Tsunehisa, S. and Takash, K.: Improvement in tool life of electroplate diamond tools by Ni-based carbon nanotube composite coatings, Precis. Eng., 38, 659–665, https://doi.org/10.1016/j.precisioneng.2014.03.003, 2014.
Wang, F.: Optimization design of impregnated diamond bit for hard formation, East China: China University of Petroleum, https://doi.org/10.7666/d.y1542950, 2009 (in Chinese with English abstract).
Yang, M.: New development of PDC bit technology, Science and Technology of West China, 9, 10–11, 2010 (in Chinese with English abstract).
Yang, Y. X. and Song, D. D.: Study of a new impregnated diamond bit for drilling in complex, highly abrasive formation, J. Petrol.Sci. Eng., 187, 106831, https://doi.org/10.1016/j.petrol.2019.106831, 2019.
Zuo, L.: Study on cutting mechanics of impregnated diamond bit, Southwest Petroleum University, https://doi.org/10.3321/j.issn:1000-5870.2002.05.012, 2015 (in Chinese with English abstract).