the Creative Commons Attribution 4.0 License.
the Creative Commons Attribution 4.0 License.
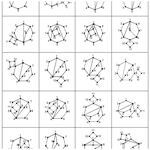
Innovative design method for planar mechanism configuration based on component similarity discrimination
Weiwei Hong
Jinxi Chen
Bingliang Ye
Rongjiang Cui
Obtaining new models of mechanical equipment to conduct mechanical innovative design through kinematic chain configuration synthesis is an effective method. However, in practice, due to the existence of similar components, existing innovative design methods easily produce redundant design schemes, which require extensive isomorphic discrimination operations, and the design process is complex. In view of existing problems, this study analyzes a method for discriminating between similar components of mechanisms from the perspective of graph theory and then applies it to the specialization of topological graphs to solve the problem of redundant design schemes. Finally, using the innovation of a drilling rig drilling arm mechanism as an example, 52 feasible schemes without redundancy are obtained. This paper provides a reference for the innovation of the configuration of planar mechanisms without design redundancy.
- Article
(2425 KB) - Full-text XML
- BibTeX
- EndNote
Mechanical innovative design is a complex and systematic process. Tsai (2000) divided the design process into three stages: product planning, conceptual design and configuration design. Among them, the conceptual design stage can best reflect human creativity in product development and is the key to the process of innovative mechanical design.
Traditional mechanical innovative design relies on designers' practical experience or intuitive inspiration, which is characterized by the lack of a systematic approach and a lack of reliability (Savage, 1972; Freudenstein and Maki, 1979; Yan and Hwang, 1991; Hung and Yan, 2008; Li and Dai, 2012). To obtain all mechanical schemes, scholars in this field have proposed an innovative design method that uses kinematic chain configuration synthesis. For example, Yang (1995) proposed the general process of mechanical innovative design, Zhang et al. (1995) applied a similarity matrix to describe the similar relationship of kinematic chain components and carried out the innovative mechanical design, and Wang et al. (2000) proposed the relation code method to discriminate the similarity of components. This method is simple, but misjudgment occurs in some special cases. In 1992, Yan Hong-sen (Yan, 1992) proposed a method for creating a mechanism scheme based on motion chain regeneration. First, all kinematic chains meeting the topological characteristics are enumerated according to the topological characteristics of the mechanism. The design rules are then formulated, and the appropriate graph structure is selected as the graphic carrier. Finally, a new mechanism scheme is obtained after specific processing. Mruthyunjaya (1984) classified the mechanical system according to the types of kinematic pairs and components, synthesized the configuration of various machines, and then applied this method to design the mechanical system of a load device and an internal force device. Nie (2008) developed a method for creating a mechanism scheme using motion chain regeneration, proposed an innovative mechanism scheme design method based on design rules, applied it to the innovative design of the continuously variable transmission and obtained a variety of transmission schemes. Huang (2016) innovatively designed a 12-bar heavy-duty hydraulic shovel excavator with 3 degrees of freedom (DOFs) and a 9-bar loader with 2 DOFs based on the comprehensive kinematic chain configuration method (Huang, 2016). Yang (2019) innovatively designed a six-speed automatic transmission based on the comprehensive motion chain structure method.
Although using kinematic chain configuration synthesis is effective for mechanism innovative design, in practical applications, due to the existence of similar components, this approach can easily produce redundant design schemes and requires a large number of isomorphic discrimination operations (Ravisankar and Mruthyunjaya, 1985; Kim and Kwak, 1990; Shin and Krishnamurthy, 1993; Hsu, 1994; Rao, 2003). However, the problem of isomorphic discrimination has not been effectively solved (Ding, 2009; Yang and Ding, 2018b; Chen et al., 2021; Sun et al., 2021). Therefore, this study examines a method for discriminating between similar components of a mechanism from the perspective of graph theory, applies it to the specialization of a topological map and uses the innovation of the drilling arm mechanism of a rock drilling jumbo as an example to verify it.
A topological diagram does not consider the scale information of components nor motion pairs; it only considers the number and type of components and motion pairs and the connection between them. In a topological diagram, the vertex represents the component, and the edge represents the motion pair. For example, Fig. 1b is the topological diagram of Fig. 1a. To facilitate computer operation, the topological graph is generally given in the form of the adjacency matrix. The definition of the adjacency matrix is shown in Eq. (1). aij represents the elements of row i and column j in the matrix. n is a matrix dimension, and the adjacency matrix is a symmetric square matrix of n rows and n columns. For example, the corresponding adjacency matrix of Fig. 1b is shown in Eq. (2).
In graph theory, the k power of the adjacency matrix represents the multiplication of several numbers of the general matrix, i.e., indicates the number of paths from vertex vi to vj through k edges to each other. For example, Eq. (3) represents the number of paths that reach the other party through two sides from 2 to 5 – that is, and .
Definition 1. Ordering the row elements of the power of the adjacency matrix in descending order is called the power value sequence of the graph, which is recorded as .
Definition 2. Comparing the element values of each column of the power value sequence in descending order is called the power value constant of the graph, which is recorded as .
For example, the fourth power sequence is and the fourth power constant is in the adjacency matrix in Fig. 1b.
Discrimination rules of similar components
When the values of the row elements of the fourth power constant matrix of the adjacency matrix are the same, the vertexes corresponding to the row elements are similar, which means that they have similar components. For example, in Eq. (5), the row element values of vertexes 3 and 4 and vertexes 7 and 8 are the same, and vertexes 3 and 4 and vertexes 7 and 8 are similar to each other. According to the vertex degree code method, proposed by Wang et al. (2000), the similarity recognition of Fig. 1b is conducted. The 10-bar motion chain requires a three-layer vertex degree sequence, , and vertexes 6, 7 and 8 are similar, which contradicts the comprehensive results of this study. The main reason for this is that the vertex degree code method only considers the vertex degree relationship and not the connection relationship.
The similarity recognition algorithm in this study is not only accurate but also efficient. The recognition of Fig. 1b takes only 5.4 ms, but the application of the permutation and combination method takes 298.9 s.
The innovative design steps of the mechanism based on similarity discrimination of the components are shown in Fig. 2 and outlined in the following.
Step 1. According to the tasks and requirements, the topological characteristics of known mechanisms are summarized and the topological diagrams are enumerated.
Existing designs that meet the designer's expectations based on the available literature are searched for as well as relevant patents and practical projects. The topological characteristics of these designs, including the mechanism type, the degrees of freedom and the number of components are summarized. It is determined if the topological diagram of the mechanism is a plan diagram. Finally, the motion chains are enumerated to obtain those with the same topological characteristics as the reference design.
Step 2. The topological map is filtered according to the machine structural and functional requirements.
According to engineering practice and the designer's requirements, the structural and functional characteristics of the known mechanism are analyzed, the topological structural requirements generated by the structural and functional constraints of the mechanism are obtained, the common topological structural elements of this kind of mechanism are restored, and an accurate and unambiguous mechanism feature description language is provided. Design constraints are extracted from the following aspects:
- i.
restrictions on component types, such as the rack can only be a certain type of component;
- ii.
restrictions on the connection type between components, such as the rack, can only be connected with certain types of components.
Step 3. Topological map customization.
According to the design requirements, specific types of components and kinematic pairs are assigned to the kinematic chain. To avoid a redundant design scheme, we have to identify the similarity of mechanical components in the specialization process – that is, we have to obtain similar components through the power value constant and then determine the mechanism frame, prime mover, actuator and other components in turn. Only components with original similarity may still have similarity, and the originally dissimilar components will not be similar.
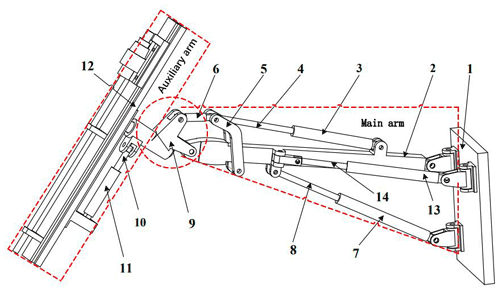
Figure 3Spatial drill arm mechanism with 4 DOFs: (1) rack, (2) main boom, (3–4) auxiliary arm angle cylinder, (5) rocker, (6) connecting rod, (7–8) main arm lift cylinder, (9) auxiliary arm connecting rod, (10–11) auxiliary arm that turns the cylinder, (12) deputy boom and (13–14) main arm swing cylinder.
Step 4. The mechanism diagram is drawn, and the known mechanism to obtain a new executable mechanism library is deleted.
In step 2, the specific topological diagram is represented in the mechanism diagram image, the existing design is deleted and the remaining scheme is the new design scheme. Before scaling synthesis, we need to analyze the advantages and disadvantages of the new design scheme structure to obtain a scheme with the same function and better performance.
Drilling rigs are key pieces of equipment for infrastructure construction and energy mining, and the drilling arm is the key execution mechanism of a drilling rig. At present, research into the innovative application of the drill arm mechanism configuration mainly relies on the practical experience of engineers and technicians, and only a few mechanism configurations have been found. In this study, the configuration synthesis method is applied to innovate the configuration design of the drill arm mechanism, and an executable mechanism library is established to provide more drill arm mechanism design choices.
Step 1. According to tasks and requirements, the topological features of known organizations are summarized and the topological diagrams are enumerated.
Figure 3 shows a commonly used spatial drill arm mechanism with 4 DOFs (Lu, 2019), and the mechanism topological model is shown in Fig. 4 (the dotted line represents the moving pair). The four actions are controlled by four respective hydraulic cylinders. The main arm swing hydraulic cylinder controls the drill arm swing, the main arm lift hydraulic cylinder controls the drill arm elevation angle, the auxiliary arm angle hydraulic cylinder controls the auxiliary arm inclination angle, and the auxiliary arm rotation hydraulic cylinder controls the auxiliary arm rotation angle. To change to a planar mechanism, the oscillating hydraulic cylinder is removed. Only the remaining planar 12-rod motion chain with 3 DOFs is integrated, and the graph theory method is applied to conduct the motion enumeration (Ding et al., 2011; Yang and Ding, 2018a).
Step 2. According to the structural and functional requirements of the roadheader, a topological diagram is selected.
- i.
Considering the mechanical stiffness, the frame should at least be connected with the main arm and the main arm lifting hydraulic cylinder – that is, at least one vertex in the topological diagram with a vertex degree greater than or equal to 2 is the frame. The frame and the main arm are connected by a lifting oil cylinder – that is, a binary chain with a length of 2 exists between the frame and the main arm.
- ii.
The original moving parts are three hydraulic cylinders (moving pairs), which means that the topological diagram has at least three binary chains with a length of 2.
- iii.
The actuator is the auxiliary arm connecting rod, and a second rod must be used as the output, which means that the topological diagram has at least one binary chain with a length of 1.
- iv.
Based on the overall layout of the drilling arm structure, the main arm should be connected to the frame, the auxiliary arm connecting rod, the rocker and the main arm lifting hydraulic cylinder, respectively; thus, the topological diagram has at least one vertex greater than or equal to 4 as the main arm.
- v.
The auxiliary boom and the auxiliary boom rotary cylinder form a spatial rotation, which means the topological diagram has at least one binary chain with a length of 3.
In summary, the topological diagram has at least two binary chains with lengths of greater than or equal to 2, one binary chain with a length of 3, at least one binary chain with a length of 1, at least one frame with a vertex degree greater than or equal to 2, and one main arm with a vertex degree greater than or equal to 4.
Step 3. Topological map specialization.
Figure 4 is used as an example to illustrate the mechanism specificity process, where ▴ represents the frame and ▪ represents the main arm.
The constant of the fourth power in Fig. 4 is calculated to obtain the potential similarity, namely Eq. (6).
According to Eq. (6), no line has the same power value, which means that there is no similarity in the graph. The frame, the original moving parts, the actuators, and other components are identified in turn.
The vertex degree of the rack is greater than or equal to two vertexes, which means that all vertexes in the topology can be used as the initial selection for the rack. The original moving part of the mechanism is the moving pair, which is side 3–4, side 7–8 and side 10–11. Vertexes 3, 4, 7, 8, 10 and 11 cannot be selected as the frame. When vertex 1 is selected as the rack, the similarity information of the graph does not change. The actuator is a binary chain with a length of 1, only vertex 6 meets the requirements and the main arm can only select vertex 2.
Each topological graph that meets the initial constraints of the structure and function is specified.
Step 4. The schematic diagram of the mechanism is drawn, the known mechanism is deleted and a new executable mechanism library is obtained.
The specific topological diagram is represented in detail by the schematic of the mechanism, the existing design is deleted and the remaining schemes are feasible new designs – 52 in total, as shown in Appendix A. Figures 5 and 6 show a respective 3D model and simulation model of a new spatial drilling arm mechanism with 4 DOFs.
The study reached the following main conclusions:
-
The innovative machine configuration design can avoid redundant schemes and improve design efficiency by using the similar component discrimination method.
-
Using the power constant to discriminate similar components does not require complex formula derivation. The operation is also simple, and engineers can easily master the computer implementation.
-
A total of 52 new configurations for a rock drilling trolley drilling arm mechanism were obtained through innovative design, providing a reference for the design of such a mechanism.
All data included in this study are available upon request from the corresponding author.
WH is the lead author of this article and was responsible for collecting the research literature, organizing the paper structure and writing the paper. JC co-authored the manuscript and provided suggestions for the revision and correction of the paper. BY and RC are the corresponding authors of this paper; they conceived the research and were responsible for writing and revising the paper.
The contact author has declared that neither they nor their co-authors have any competing interests.
Publisher's note: Copernicus Publications remains neutral with regard to jurisdictional claims in published maps and institutional affiliations.
The authors thank the reviewers for their critical and constructive review of the article.
This research has been supported by the National Natural Science Foundation of China (grant nos. 51805306 and 32171899).
This paper was edited by Daniel Condurache and reviewed by two anonymous referees.
Chen, J., Ding, J., Hong, W., and Cui, R.: Structural synthesis of plane kinematic chain inversions without detecting isomorphism, Mech. Sci., 12, 1061–1071, https://doi.org/10.5194/ms-12-1061-2021, 2021.
Ding, H. F.: Isomorphism identification of graphs: Especially for the graphs of kinematic chains, Mech. Mach. Theory, 44, 122–139, https://doi.org/10.1016/j.mechmachtheory.2008.02.008, 2009.
Ding, H. F., Hou, F., and Kecskeméthy, A.: Synthesis of a complete set of contracted graphs for planar non-fractionated simple-jointed kinematic chains with all possible DOFs, Mech. Mach. Theory, 46, 1588–1600, https://doi.org/10.1016/j.mechmachtheory.2011.07.012, 2011.
Freudenstein, F. and Maki, E. R.: The creation of mechanisms according to kinematic structure and function, Environ. Plann. B, 6, 375–391, https://doi.org/10.1068/b060375, 1979.
Hsu, C. H.: Displacement isomorphism of planetary gear trains, Mech. Mach. Theory, 29, 513–523, https://doi.org/10.1016/0094-114X(94)90091-4, 1994.
Huang, P.: Research on the structural synthesis theory and technology of the planar multi-loop coupled mechanisms, Master thesis, Yanshan University, Qinhuangdao, https://kns.cnki.net/kcms/detail/detail.aspx?FileName=1017808497.nh&DbName=CDFD2018 (last access: 11 April 2022), 2016.
Hung, C. C. and Yan, H.-S.: A procedure to count the number of planar mechanisms subject to design constraints from kinematic chains, Mech. Mach. Theory, 43, 676–694, https://doi.org/10.1016/j.mechmachtheory.2007.06.009, 2008.
Kim, J. U. and Kwak, B. M.: Application of edge permutation group to structural synthesis of epicyclic gear trains, Mech. Mach. Theory, 25, 563–574, https://doi.org/10.1016/0094-114X(90)90070-Z, 1990.
Li, S. J. and Dai, J. S.: Structural synthesis method of planar mechanisms using the assur-group based adjacency matrix, Chin. J. Mech. Eng.-En., 48, 13–18, 2012.
Lu, F. W.: Structure synthesis and innovative design of drilling arm mechanism of rock drilling robot based on graph theory, Master thesis, Zhejiang Sci-Tech university, Hangzhou, https://doi.org/10.27786/d.cnki.gzjlg.2020.000852, 2019.
Mruthyunjaya, T. S.: Kinematic structure of mechanical srcvisited, Mech. Mach. Theory, 19, 507–530, https://doi.org/10.1016/0094-114X(84)90057-0, 1984.
Nie, S. H.: Research on panar mechanism type synthesis and innovation scheme designs, Master thesis, Xi 'an University of Technology, Xi'an, https://kns.cnki.net/kcms/detail/detail.aspx?FileName=2008160899.nh&DbName=CDFD2008 (last access: 11 April 2022), 2008.
Rao, A. C.: A genetic algorithm for epicyclic gear trains, Mech. Mach. Theory, 38, 135–147, https://doi.org/10.1016/s0094-114x(02)00094-0, 2003.
Ravisankar, R. and Mruthyunjaya, T. S.: Computerized synthesis of the structure of geared kinematic chains, Mech. Mach. Theory, 20, 367–387, https://doi.org/10.1016/0094-114X(85)90042-4, 1985.
Savage, M.: Four-link mechanisms with cylindric, revolute and prismatic pairs, Mech. Mach. Theory, 7, 191–210, https://doi.org/10.1016/0094-114X(72)90004-3, 1972.
Shin, J. K. and Krishnamurthy, S.: Standard code technique in the enumeration of epicyclic gear trains, Mech. Mach. Theory, 28, 347–355, https://doi.org/10.1016/0094-114X(93)90075-7, 1993.
Sun, W., Li, R., Kong, J., and Li, A.: A new method for isomorphism identification of planetary gear trains, Mech. Sci., 12, 193–202, https://doi.org/10.5194/ms-12-193-2021, 2021.
Tsai, L. W.: Mechanism design: enumeration of kinematic structures according to function, CRC Press, London, https://doi.org/10.1115/1.1334346, 2000.
Wang, Y., Sai, J., and Yan, H.-S.: Distinguishing the similarity of links by relation code method, J. Tianjin. Univ., 33, 290–293, 2000.
Yan, H.-S.: A methodology for creative mechanism design, Mech. Mach. Theory, 27, 235–242, https://doi.org/10.1016/0094-114X(92)90013-8, 1992.
Yan, H.-S. and Hwang, Y. W.: The specialization of mechanisms, Mech. Mach. Theory, 26, 541–551, https://doi.org/10.1016/0094-114X(91)90037-5, 1991.
Yang, T. L.: Basic theory of mechanical systems-structure-kinematics dynamics, China Machine Press, Beijing, ISBN 7-111-04966-7, 1995.
Yang, W. J.: Automatic Synthesis of Planetary Gear Trains and Plane Linkage Kinematic Chains and Creative Design of Equipment, PhD thesis, China university of geosciences, Wuhan, https://doi.org/10.27492/d.cnki.gzdzu.2019.000215, 2019.
Yang, W. J. and Ding, H. F.: The complete set of one-degree-of-freedom planetary gear trains with up to nine links, J. Mech. Design, 141, 043301, https://doi.org/10.1115/1.4041482, 2018a.
Yang, W. J. and Ding, H. F.: The perimeter loop-based method for the automatic isomorphism detection in planetary gear trains, J. Mech. Design, 140, 123302, https://doi.org/10.1115/1.4041572, 2018b.
Zhang, Y., Wang, Y., and Lu, Y.: Similarity analysis of kinetic chains and its application in mechanism type synthesis, J. Tianjin. Univ., 29, 551–558, 1996.
- Abstract
- Introduction
- The similar component discrimination method
- Innovative design steps of a mechanism based on component similarity discrimination
- Application example
- Conclusions
- Appendix A: New structural design graphs
- Data availability
- Author contributions
- Competing interests
- Disclaimer
- Acknowledgements
- Financial support
- Review statement
- References
- Abstract
- Introduction
- The similar component discrimination method
- Innovative design steps of a mechanism based on component similarity discrimination
- Application example
- Conclusions
- Appendix A: New structural design graphs
- Data availability
- Author contributions
- Competing interests
- Disclaimer
- Acknowledgements
- Financial support
- Review statement
- References